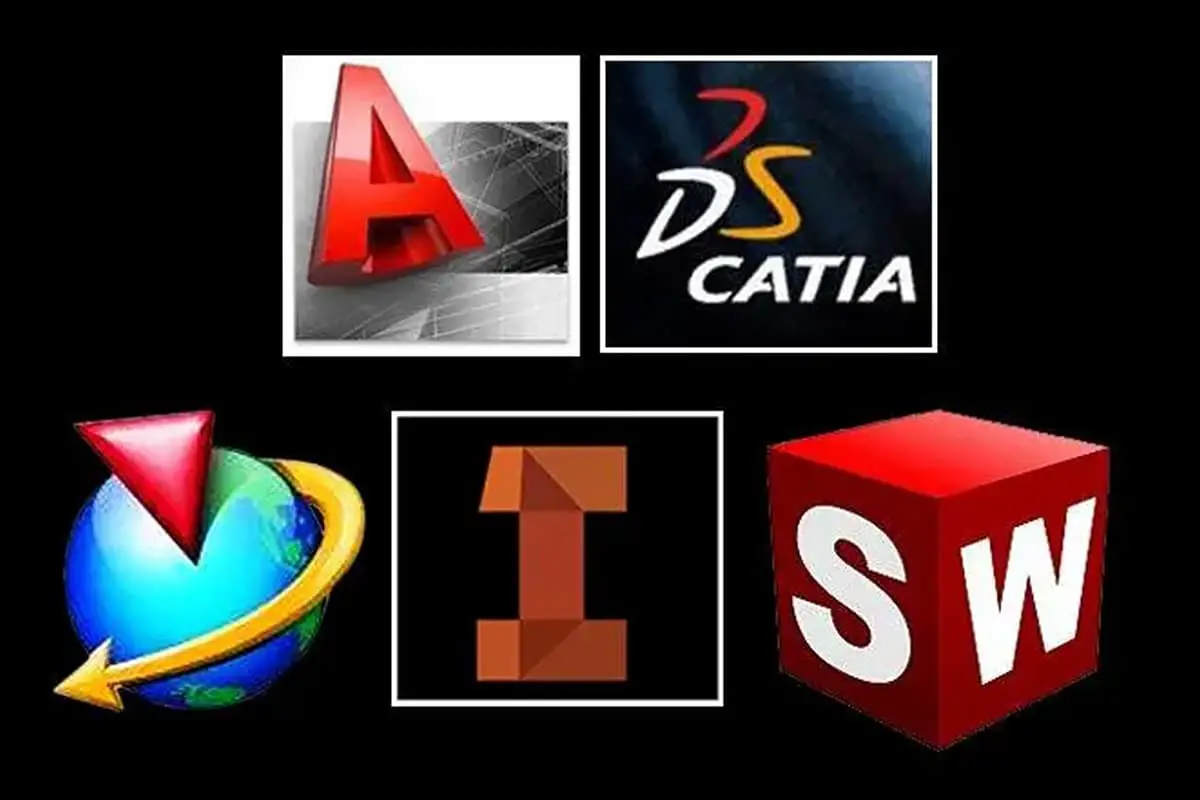
Vous êtes-vous déjà demandé comment l'impression 3D a évolué pour révolutionner la fabrication ? Cet article présente les principaux processus et caractéristiques de l'impression 3D, depuis ses origines avec les techniques de poudre et de liant jusqu'à ses applications modernes pour la création de pièces complexes et fonctionnelles. Vous apprendrez comment fonctionnent des innovations telles que le jet de liant et découvrirez les avantages et les limites de cette technologie transformatrice. Découvrez comment l'impression 3D continue de façonner les industries grâce à sa capacité à produire des produits détaillés, personnalisables et rentables.
Utilisant des matériaux en poudre pour l'impression 3D, le processus SLS susmentionné est relativement coûteux en raison de l'utilisation de lasers. Cependant, l'utilisation d'un agent liant pour faire adhérer les particules de poudre et construire des couches pour former des formes est théoriquement valable. Le 20 avril 1993, le professeur Emanuel Sachs et son équipe du MIT ont obtenu un brevet américain pour les "techniques d'impression tridimensionnelle", connues sous le nom de 3DP.
L'invention s'inspire des imprimantes à jet d'encre, très répandues à l'époque, qui remplacent l'encre des cartouches par un liant liquide. En extrudant ce liant sur un lit de poudre en vrac à l'aide de la tête d'impression, il était possible d'imprimer des objets tridimensionnels. De même, en utilisant des liants de couleur primaire et une correspondance numérique précise des couleurs, il était possible d'imprimer en couleur sur la poudre, comme on le fait avec l'impression à jet d'encre sur le papier.
Ce processus d'impression 3D ressemble beaucoup aux imprimantes conventionnelles, et le titre de son brevet, "impression 3D", est simple et facile à comprendre. Auparavant, la technologie d'impression 3D était connue sous le nom de prototypage rapide. Depuis, le terme "impression 3D" a gagné en popularité et toutes les technologies de prototypage rapide sont communément appelées "impression 3D", les appareils eux-mêmes étant appelés "imprimantes 3D".
En 2012, l'American Society for Testing and Materials (ASTM) a défini ce procédé d'impression 3D sous le nom de "Binder Jetting" dans sa norme terminologique relative à la fabrication additive (ASTM F2792-12a).
En théorie, le processus de projection de liant peut être utilisé pour imprimer en 3D divers matériaux en poudre tels que les céramiques, les métaux, le gypse, les plastiques et le sable. En 1995, Z Corporation a été créée avec une licence du MIT et s'est concentrée sur la commercialisation de la projection de liant avec de la poudre de gypse.
Depuis 1997, elle a lancé une série d'imprimantes à jet de liant, dont l'imprimante monochrome d'entrée de gamme ZPrinter 310 Plus et, en 2005, la première imprimante 3D couleur au monde, la Spectrum Z510, comme le montre la figure 5-31 avec l'imprimante couleur et ses modèles imprimés. Cette imprimante a marqué une étape importante dans l'évolution de l'impression 3D, en la rendant vivante et colorée. En 2012, Z Corporation a été rachetée par 3D Systems, qui a poursuivi le développement de la série d'imprimantes Color-Jet.
Les spécifications de la série Color-Jet actuellement vendue sur le site Web de 3D Systems sont indiquées dans le tableau 5-1.
Tableau 5-1 : Spécifications officielles de 3D Systems pour les imprimantes de la série Color-Jet.
Modèle | ProJet260C | ProJet360 | ProJet 460Plus | ProJet660Pro | ProJet860Pro |
Couleur | Couleur de base (CMJ) | Monochrome (blanc) | Couleur de base (CMJ) | Couleur (CMYK) | Couleur de base (CMJ) |
Épaisseur de la couche/mm | 0.1 | 0.1 | 0.1 | 0.1 | 0.1 |
Résolution/dpi | 300×450 | 300×450 | 300×450 | 600×540 | 600×540 |
Dimensions de l'impression/mm | 236×185×127 | 203×254×203 | 203×254×203 | 254×381×203 | 508×381×229 |
Vitesse d'impression/(mm/h) | 20 | 20 | 23 | 28 | 5~15 |
Nombre de têtes d'impression | 2 (HP57+HP11) | 1 (HP11) | 2(HPS7+HP11) | 5(HP11) | 5(HP11) |
Nombre de buses | 604 | 304 | 604 | 1520 | 1520 |
En 1996, Extrude Hone Corporation a obtenu une licence du MIT pour la recherche et la commercialisation de matériaux en poudre métallique formés par projection de liant. En 1997, elle a lancé le premier appareil de projection de liant en poudre métallique au monde, le ProMetal RTS-300.
En 2003, la société ExOne a émergé d'Extrude Hone, se concentrant uniquement sur l'industrie de l'impression 3D, puis lançant la première imprimante 3D à grès au monde, la S15. Depuis lors, ExOne s'est spécialisée dans la projection de liant pour les matériaux métalliques et le grès, devenant progressivement un leader de la technologie 3DP. La figure 5-32 montre l'imprimante Innovent+ d'ExOne et certains des modèles métalliques imprimés par l'entreprise.
Fondée en 1999, la société allemande Voxeljet a également obtenu une licence du MIT et s'est consacrée au développement d'imprimantes 3D à sable pour le moulage de moules. L'entreprise utilise la technologie du jet de liant pour imprimer des moules en sable destinés à être utilisés dans les processus traditionnels de moulage des métaux.
Ces dernières années, la technologie de projection de liant a suscité un intérêt croissant en Chine, avec des entreprises telles que Wuhan Yizhi Technology Co. Ltd, Aisikai Technology Co. Ltd, Guangdong Fenghua Zhuoli Technology Co. Ltd et Ningxia Sharing Group qui ont pris les devants.
En outre, une équipe de l'Université des sciences et technologies de Huazhong mène des recherches sur la technologie de projection de liant depuis 2012, en se concentrant initialement sur l'impression avec du gypse, des polymères et du sable de coulée, et actuellement sur la technologie de projection de liant métallique. En 2017, en collaboration avec Wuhan Yizhi Technology Co., Ltd, ils ont présenté une imprimante à jet de liant métallique capable d'imprimer avec des matériaux tels que le plâtre, les polymères et le sable de coulée. Acier inoxydable 316LAcier inoxydable, 420, cuivre et alliages de titane.
Vous trouverez ci-dessous un tableau comparatif des détails techniques de certaines entreprises nationales et internationales qui développent une technologie de projection de liants métalliques.
Tableau 5-2 : Tableau comparatif des détails techniques des technologies de formage par pulvérisation d'adhésifs métalliques de certaines entreprises de R&D nationales et internationales
Entreprise | Vitesse d'impression (cm3/h) | Volume de construction | Matériaux disponibles | Densité /% | Résolution /dpi | Épaisseur de la couche /μm |
Métal numérique | 100 | 203mm×180mm×69mm | ACIER INOXYDABLE : 316L, 17-4 | 96 | - | 30~200 |
Exone | Jusqu'à 10 000 | 800mm×500mm×400mm | SS:316L,304 | 96~99 | 600~1200 | 30~200 |
Bureau en métal | 12000 | 750mm×330mm×250mm | - | 一 | 一 | 50 |
HP | – | 430mm×320mm×200mm | ACIER INOXYDABLE : 316L | >93 | 1200 | 50~100 |
GE | – | – | ACIER INOXYDABLE : 316L | – | 一 | – |
3DEO | – | – | SS : 17-4 | 99 | - | – |
Wuhan Yizhi | – | 500mm×450mm×400mm | ACIER INOXYDABLE : 316, 420 | 95~99 | 600 | 50~200 |
L'examen du schéma abstrait du brevet 3DP du professeur Emanuel Sachs, tel qu'illustré à la figure 5-33, présente des informations essentielles : "...produire une couche de matériau en poudre lié..." indique la création d'une couche de matériau en poudre lié par le biais d'un processus d'accumulation couche par couche à l'aide de matériau en poudre.
La question se pose de savoir comment la poudre est mise en forme : "...déposer un matériau liant..." suggère qu'au lieu d'utiliser un laser, un matériau liant est distribué dans des zones sélectionnées de chaque couche, liant la poudre en forme. Le résumé indique également que le matériau peut être "...traité ultérieurement, par exemple en le chauffant..." pour en améliorer la résistance.
La figure 5-34 illustre le processus 3DP, détaillé comme suit :
① Préparation des données. Obtenir un modèle tridimensionnel de la pièce et le traiter en tranches bidimensionnelles.
② Mise en place de la poudre. La poudre est stockée soit dans une trémie, soit dans un cylindre d'alimentation, avec deux méthodes d'application : la trémie libère une certaine quantité de poudre sur le lit de poudre par le haut, appelée méthode d'alimentation, tandis que le cylindre d'alimentation distribue une quantité prédéfinie de poudre en élevant le piston d'alimentation à une certaine hauteur, appelée méthode de mise en place de la poudre, comme le montre la figure 5-34(a) et (b).
Un rouleau étale et compacte ensuite la poudre sur la zone de formation du lit de poudre.
③ Mouvement bidimensionnel. La tête d'impression, chargée de liant, est commandée par le fichier de commandes pour se déplacer dans les directions X et Y, en pulvérisant du liant pour lier la poudre à la forme. Les zones non pulvérisées restent libres et servent de support aux couches suivantes (pour l'impression de modèles colorés, trois liants de couleur primaire sont utilisés).
④ Mouvement dans la direction Z. Le lit de poudre descend d'une couche dans la direction Z, la zone de formage est remplie d'une nouvelle couche de poudre et la couche de poudre est maintenue à niveau.
⑤ Liaison entre les couches. La tête d'impression se déplace selon de nouvelles commandes X et Y, pulvérisant du liant pour donner forme à la couche de poudre en cours tout en la faisant adhérer à la couche supérieure, ce qui permet d'obtenir une liaison entre les couches.
⑥ Répéter le processus ci-dessus jusqu'à l'obtention de la pièce tridimensionnelle finale.
La poudre inutilisée de l'impression 3DP, qui n'est ni préchauffée ni exposée à une irradiation laser, peut être entièrement recyclée pour être réutilisée, ce qui permet théoriquement d'atteindre un taux d'utilisation des matériaux de 100%. Après l'impression 3D, les pièces nécessitent un post-traitement, qui comporte généralement trois étapes :
Les pièces étant entièrement recouvertes de poudre, il est nécessaire d'enlever la poudre résiduelle à la surface de la pièce dans une boîte à gants à l'aide de brosses, de pistolets à air comprimé, etc., afin de la recycler et de la réutiliser lors d'une impression ultérieure.
Les pièces imprimées en 3DP contiennent souvent de nombreux pores et sont relativement faibles, ce qui nécessite un post-traitement pour les renforcer. Pour les pièces imprimées avec des matériaux inorganiques en poudre comme le gypse, différents infiltrants à durcissement instantané sont sélectionnés en fonction de l'utilisation prévue pour pénétrer dans les pièces.
Par exemple, les infiltrants adaptés aux modèles colorés peuvent améliorer la résistance, la couleur et la stabilité de la couleur ; les infiltrants binaires pour les modèles fonctionnels peuvent améliorer considérablement la résistance du modèle ; et les infiltrants respectueux de l'environnement peuvent être utilisés pour l'imprégnation ou la pulvérisation afin d'améliorer la dureté et le module de la surface.
Les pièces imprimées à partir de poudres métalliques nécessitent généralement des étapes supplémentaires de post-traitement telles que le dégraissage, le frittage à haute température, le pressage isostatique à chaud, l'infiltration ou l'imprégnation de cuivre pour augmenter la résistance et la densité de la pièce.
Généralement, une combinaison de sablage, de polissage, de peinture et d'usinage est utilisée pour améliorer la qualité et la précision de la surface de la pièce, ainsi que son aspect lisse et sa couleur.
Le processus 3DP présente cinq avantages notables :
La technologie 3DP permet l'impression en couleur et exprime parfaitement la créativité de la conception des produits en couleur. Elle est largement utilisée dans les domaines de la créativité culturelle, du cinéma, de l'animation et d'autres domaines.
Le processus 3DP permet d'imprimer avec presque tous les matériaux en poudre, y compris les poudres métalliques, ce qui élargit considérablement ses applications fonctionnelles.
La poudre non liée sert de support naturel, éliminant le besoin de supports auxiliaires supplémentaires, ce qui se traduit par une efficacité d'impression élevée et des coûts de matériaux réduits au cours du processus d'impression.
Le processus 3DP n'impose pratiquement aucune restriction quant à la complexité des pièces, ce qui permet la production de différents types de pièces. formes complexes telles que les pièces poreuses, les pièces évidées et les pièces emboîtées. Il convient au développement de nouveaux produits ou à la production de pièces individuelles ou en petites séries.
D'une part, le processus 3DP n'utilise pas de laser, ce qui réduit les coûts d'exploitation et de maintenance de l'équipement ; d'autre part, ses têtes de projection de liant peuvent effectuer un balayage en réseau plutôt qu'un balayage de points au laser, ce qui se traduit par une grande efficacité d'impression et un faible coût.
Cependant, le processus 3DP présente également certaines limites et certains inconvénients :
La résistance et la ténacité sont relativement faibles et ne conviennent généralement qu'aux présentoirs d'échantillons ou aux moules de coulée (tels que les moules en sable). Les essais fonctionnels ne sont pas viables et les pièces imprimées en métal nécessitent un frittage supplémentaire et une infiltration de cuivre dans un four de frittage pour atteindre la résistance et la densité finales.
Comme les pièces sont formées par liage de poudre, la surface présente une certaine texture granuleuse, ce qui rend difficile l'obtention du caractère lisse des pièces imprimées avec les techniques de photopolymérisation.
Étant donné que le stockage sur lit de poudre est utilisé et compte tenu de l'activité de surface des matériaux en poudre, le stockage des matériaux en vrac est important et difficile. Le mécanisme d'alimentation de la trémie, bien qu'il permette de résoudre en partie les problèmes de stockage, ne modifie pas le principe fondamental du stockage sur lit de poudre.