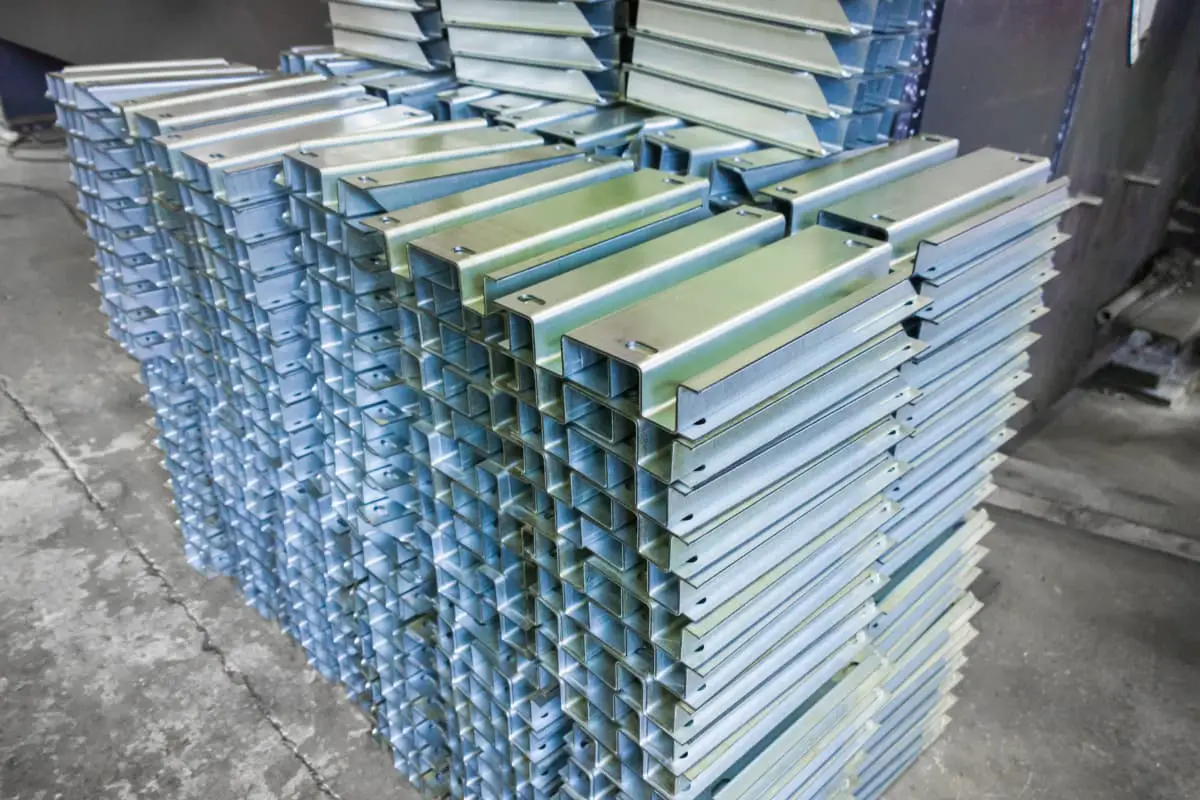
Vi siete mai chiesti quale sia l'arte e la scienza che si cela dietro gli eleganti involucri metallici dei vostri gadget preferiti? In questo post ci immergeremo nell'affascinante mondo della lavorazione della lamiera. In qualità di ingegnere meccanico esperto, condividerò le mie conoscenze sui materiali, i processi e i principi di progettazione che trasformano le lamiere piatte nelle forme complesse che ospitano i nostri dispositivi elettronici moderni. Preparatevi a esplorare le tecniche all'avanguardia e la risoluzione creativa dei problemi che rendono la lavorazione della lamiera una parte fondamentale dello sviluppo dei prodotti.
La fabbricazione di lamiere è un processo completo di lavorazione a freddo di lamiere sottili, in genere di spessore inferiore a 6 mm. Questo versatile metodo di produzione comprende un'ampia gamma di operazioni, tra cui cesoiatura, tranciatura, piegatura, saldatura, rivettatura, formatura e trattamenti superficiali. La caratteristica distintiva della lavorazione della lamiera è lo spessore uniforme mantenuto in ogni componente.
Il processo di fabbricazione delle lamiere può essere classificato a grandi linee in due approcci principali:
Ciascun approccio presenta vantaggi distinti e la scelta dipende da fattori quali il volume di produzione, la complessità del pezzo, le proprietà del materiale e le considerazioni economiche. La moderna fabbricazione di lamiere spesso integra entrambi i metodi, sfruttando i punti di forza di ciascuno di essi per ottimizzare l'efficienza, la qualità e l'efficacia dei costi nei vari requisiti di produzione.
I materiali in lamiera sono i più utilizzati nella progettazione strutturale dei prodotti di comunicazione.
Comprendere le prestazioni complessive dei materiali e la corretta selezione del materiale hanno un impatto importante sul costo del prodotto, sulle prestazioni, sulla qualità e sulla lavorabilità del prodotto.
1) Utilizzare materiali metallici comuni per ridurre le specifiche dei materiali e controllarli il più possibile all'interno del manuale dei materiali dell'azienda;
2) Nello stesso prodotto, ridurre il più possibile la varietà di materiali e le specifiche di spessore delle lastre;
3) Con la premessa di garantire la funzionalità dei componenti, cercare di utilizzare materiali economici, ridurre il consumo di materiali e ridurre il costo dei materiali;
4) Per l'armadietto e alcune scatole di derivazione di grandi dimensioni, è necessario prendere in considerazione la possibilità di ridurre il peso dell'intera macchina;
5) Oltre alla premessa di garantire la funzione dei pezzi, bisogna anche considerare che le prestazioni di stampaggio del materiale devono soddisfare i requisiti di lavorazione per garantire la razionalità e la qualità della lavorazione dei prodotti.
Piastra d'acciaio
1) Lamiera d'acciaio laminata a freddo
La lamiera di acciaio laminata a freddo è l'abbreviazione di lamiera di acciaio strutturale al carbonio laminata a freddo.
Da un nastro di acciaio strutturale al carbonio laminato a caldo, viene ulteriormente laminato a freddo in una lastra di acciaio di spessore inferiore a 4 mm.
Poiché la laminazione avviene a temperatura normale, non si producono scaglie di ossido di ferro. Pertanto, la qualità superficiale della lamiera fredda è buona e la precisione dimensionale è elevata.
Inoltre, il processo di ricottura ha migliori proprietà meccaniche e prestazioni di processo rispetto a acciaio laminato a caldo fogli.
I tipi comunemente utilizzati sono l'acciaio a basso tenore di carbonio 08F e l'acciaio 10#, che hanno una buona qualità. tranciatura e le proprietà di flessione.
2) Lamiera d'acciaio laminata a freddo con zincatura continua
Lamiera di acciaio laminata a freddo con zincatura continua, ovvero "lamiera elettrolitica".
Si riferisce al processo di deposito continuo di zinco da una soluzione acquosa di sale di zinco in un nastro di acciaio pre-preparato per ottenere uno strato superficiale galvanizzato sotto l'azione di un campo elettrico su una linea di elettrozincatura.
A causa dei limiti del processo, il rivestimento è sottile.
3) Lamiera d'acciaio continua zincata a caldo
La lamiera di acciaio zincata a caldo in continuo viene definita lamiera zincata o banda stagnata.
Le lamiere e i nastri di acciaio zincato a caldo continui laminati a freddo con uno spessore compreso tra 0,25 e 2,5 mm vengono prima sottoposti a un forno di preriscaldamento riscaldato a fiamma per bruciare l'olio residuo superficiale.
Contemporaneamente, sulla superficie si forma una pellicola di ossido di ferro.
Quindi, viene riscaldato a 710~920 °C in un forno di ricottura a riduzione contenente gas misti H2 e N2 per ridurre il film di ossido di ferro in ferro spugnoso.
Dopo che il nastro attivato e purificato in superficie viene raffreddato a una temperatura leggermente superiore a quella dello zinco fuso, entra nella pentola dello zinco a 450-460 °C.
Lo spessore dello strato di zinco è controllato da un coltello ad aria compressa.
Infine, adottare il trattamento di passivazione con soluzione di cromato per migliorare la resistenza alla ruggine bianca.
Rispetto alla superficie della lamiera elettrozincata, il rivestimento è più spesso e viene utilizzato principalmente per le parti in lamiera che richiedono un'elevata resistenza alla corrosione.
4) Piastra in alluminio-zinco
Il rivestimento in lega di alluminio-zinco della piastra di alluminio-zinco è composto da 55% di alluminio, 43,4% di zinco e 1,6% di silicio a 600°C.
Ha formato un denso strato protettivo di cristalli quaternari con un'eccellente resistenza alla corrosione, la normale durata di vita fino a 25 anni, 3-6 volte più lunga di una lamiera zincata e paragonabile all'acciaio inossidabile.
La resistenza alla corrosione della piastra alluminio-zinco deriva dalla funzione di barriera dell'alluminio e dalla protezione sacrificale dello zinco.
Quando lo zinco viene sacrificato per rifinire, graffiare e scalfire il rivestimento, l'alluminio forma uno strato di ossido insolubile che funge da barriera.
Le lastre di acciaio di cui sopra (2), 3) e 4) sono denominate collettivamente lamiere di acciaio rivestite e sono ampiamente utilizzate nelle apparecchiature di comunicazione.
Dopo il rivestimento lamiera d'acciaio è lavorato, non può più essere galvanizzato o verniciato.
L'incisione può essere utilizzata direttamente senza trattamenti speciali, mentre per migliorare la resistenza alla ruggine dell'incisione è possibile eseguire uno speciale trattamento di fosfatazione.
Dall'analisi dei costi, viene utilizzata la lamiera d'acciaio elettrozincata continua e l'impianto di lavorazione non deve inviare i pezzi alla galvanica, risparmiando così i tempi di placcatura e i costi di trasporto.
Inoltre, i pezzi non vengono decapati prima della spruzzatura, migliorando così l'efficienza della lavorazione.
5) Acciaio inox piastra
Grazie alla sua forte resistenza alla corrosione, alla buona conducibilità elettrica, all'elevata resistenza, ecc.
Ma dobbiamo anche considerare i suoi difetti:
Piastre in alluminio e leghe di alluminio
Le lamiere in alluminio e in lega di alluminio comunemente utilizzate sono composte principalmente dai seguenti tre materiali:
L'alluminio antiruggine 3A21, che è il vecchio marchio LF21, è una lega AL-Mn. È l'alluminio antiruggine più utilizzato.
La resistenza di questa lega non è elevata (solo superiore a quella dell'alluminio puro industriale) e non può essere trattata termicamente e rafforzata.
Pertanto, il metodo di lavorazione a freddo è spesso utilizzato per migliorare le sue proprietà meccaniche, e ha un'elevata plasticità allo stato ricotto, e la plasticità è buona nella tempra semi-fredda.
Ha una bassa plasticità, una buona resistenza alla corrosione e un'ottima saldabilità durante la tempra a freddo.
L'alluminio antiruggine 5A02 è il vecchio marchio di alluminio antiruggine AL-Mg della serie LF2.
Rispetto al 3A21, il 5A02 presenta una maggiore resistenza, soprattutto ad alta resistenza alla fatica, elevata plasticità e resistenza alla corrosione.
Il trattamento termico non può essere rafforzato e la saldabilità con la saldatura a contatto e con l'atomo di idrogeno è buona, e c'è una tendenza alla formazione di cricche cristalline durante la saldatura. saldatura ad arco di argone la lega tende a formare cricche cristalline durante l'indurimento a freddo.
La lega ha una buona lavorabilità allo stato di tempra a freddo e semicrudo, mentre la lavorabilità è scarsa allo stato ricotto e può essere lucidata.
L'alluminio duro 2A06 è il vecchio LY6, un tipo di alluminio duro comunemente usato.
L'alluminio duro e l'alluminio super-duro hanno una maggiore forza e durezza rispetto alle leghe di alluminio ordinarie, e può essere utilizzato come materiale per alcuni pannelli.
Tuttavia, la plasticità è scarsa, non è possibile eseguire la piegatura e la piegatura può causare crepe o incrinature nella parte esterna arrotondata.
Esistono nuovi standard per il grado e lo stato della lega di alluminio. Il codice standard del metodo di rappresentazione del grado è GB/T16474-1996, il codice di stato è GB/T16475-1996 e la tabella di confronto con il vecchio standard è riportata nella Tabella 1-1:
Tabella 1-1 Tabella di confronto tra nuovo e vecchio gradi di lega di alluminio
Grado | Stati | ||||||||
Nuovo | Vecchio | Nuovo | Vecchio | Nuovo | Vecchio | Nuovo | Vecchio | Nuovo | Vecchio |
1070A | L1 | 5A06 | LF6 | 2A80 | LD8 | 2A14 | LD10 | H12 | R |
1060 | L2 | 5A12 | LF12 | 2A90 | LD9 | 2A50 | LD5 | O | M |
1050A | L3 | 8A06 | L6 | 4A11 | LD11 | 6A02 | LD2 | T4 | CZ |
1035 | L4 | 3A21 | LF21 | 6063 | LD31 | 7A04 | LC4 | T5 | RCS |
1200 | L5 | 2A02 | LY2 | 6061 | LD30 | 7A09 | LC9 | T6 | CS |
5A02 | LF2 | 2A06 | LY6 | 2A11 | LY11 | ||||
5A03 | LF3 | 2A16 | LY16 | 2A12 | LY12 | ||||
5A05 | LF5 | 2A70 | LD7 | 2A13 | LY13 |
Piastre in rame e leghe di rame
Esistono due tipi principali di lastre di rame e leghe di rame comunemente utilizzate: il rame T2 e l'ottone H62.
Il rame T2 è il rame puro più comunemente utilizzato. Ha un aspetto violaceo e viene anche chiamato rame. Ha un'elevata conducibilità elettrica e termica, una buona resistenza alla corrosione e una buona formabilità.
Ma la resistenza e la durezza sono molto inferiori a quelle dell'ottone e il prezzo è molto elevato.
Viene utilizzato principalmente come elemento di corrosione per i prodotti conduttivi, di conduzione del calore e di consumo. Viene generalmente utilizzato per le parti dell'alimentazione che devono trasportare grandi correnti.
Il rass H62, un ottone ad alto tenore di zinco, ha un'elevata resistenza e un'eccellente lavorabilità a freddo e a caldo ed è facilmente utilizzabile per diverse forme di lavoro con la stampa e taglio.
Utilizzato principalmente per vari tipi di imbutitura e forza di flessione parti, la sua conduttività non è buona come quella del rame, ma ha una migliore resistenza e durezza, e il prezzo è relativamente moderato.
Per soddisfare i requisiti di conducibilità elettrica, si utilizza il più possibile l'ottone H62 al posto del rame, riducendo così notevolmente il costo del materiale.
Ad esempio, le sbarre, la maggior parte delle sbarre attuali sono realizzate in ottone H62, che si è dimostrato pienamente soddisfacente.
Esistono tre principali tipi di lamiera lavorazione: punzonatura e tranciatura, piegatura e stiratura.
Le diverse tecniche di lavorazione hanno requisiti diversi per la lastra.
La scelta della lamiera deve basarsi anche sulla forma generale e sulla tecnologia di lavorazione del prodotto.
L'impatto dei materiali sulla tranciatura
La tranciatura richiede che il foglio sia sufficientemente plastico per garantire che non si rompa durante la perforazione.
I materiali morbidi (come l'alluminio puro, l'alluminio antiruggine, l'ottone, il rame, l'acciaio a basso tenore di carbonio, ecc.) hanno buone prestazioni di punzonatura e dopo la punzonatura si possono ottenere pezzi con sezione trasversale liscia e inclinazione ridotta;
Materiali duri (come acciaio ad alto tenore di carbonioacciaio inox, alluminio duro, alluminio super-duro, ecc.) hanno una qualità scadente dopo la punzonatura e le irregolarità della sezione sono notevoli, soprattutto per le lamiere spesse.
Per i materiali fragili, è probabile che si verifichino strappi dopo la punzonatura e, in particolare, nel caso di larghezza ridotta, è probabile che si verifichino strappi.
L'effetto dei materiali sulla flessione
Le piastre che devono essere piegate e formate devono avere una plasticità sufficiente e un basso limite di snervamento.
Una lastra altamente plastica che è meno incline a rompersi quando viene piegata.
Le lastre con un limite di snervamento e un modulo di elasticità più bassi hanno meno ritorno a molla deformazione dopo la piegatura, ed è facile ottenere una forma curva accurata.
Materiali plastici come l'acciaio a basso tenore di carbonio, l'ottone e l'alluminio con un contenuto di carbonio di <0,2% sono facilmente piegabili e formabili;
I materiali più fragili, come il bronzo fosforoso (QSn6,5 ~ 2,5), l'acciaio per molle (65Mn), l'alluminio duro, l'alluminio super-duro, ecc. raggio di curvatura (r / t) durante la piegatura, altrimenti è probabile che si verifichino cricche durante la piegatura.
Occorre prestare particolare attenzione alla scelta dello stato duro e morbido del materiale, che ha una grande influenza sulle proprietà di piegatura.
Per molti materiali fragili, la flessione può causare la fessurazione o addirittura la rottura del raggio esterno.
Esistono anche piastre di acciaio con un contenuto di carbonio più elevato.
Se si sceglie uno stato duro, la piegatura causerà anche la fessurazione o addirittura la rottura del raggio esterno.
Queste dovrebbero essere evitate il più possibile.
Effetto dei materiali sulla lavorazione del disegno
La stesura della lastra, soprattutto quella in profondità, è difficile da realizzare. lavorazione della lamiera processo.
Non solo la profondità dell'allungamento deve essere la più piccola possibile, ma anche la forma deve essere il più semplice possibile e liscia. Inoltre, è necessario che il materiale abbia una buona plasticità.
In caso contrario, l'intera parte si deforma facilmente, si raggrinzisce parzialmente o viene addirittura tirata nella parte di stiramento.
Il limite di snervamento è basso e il coefficiente direzionale dello spessore della piastra è elevato.
Quanto più piccolo è il rapporto di snervamento σs/σb della lamiera, tanto migliori sono le prestazioni di punzonatura e maggiore è il limite della deformazione primaria.
Quando il coefficiente di direttività dello spessore della piastra è >1, la deformazione in direzione della larghezza è più facile di quella in direzione dello spessore.
Maggiore è il valore del raggio di stiramento R, minore è la probabilità di assottigliamento e frattura durante il processo di stiramento e migliori sono le proprietà di trazione.
Le proprietà di trazione comuni sono: lamiera di alluminio puro, 08Al, ST16, SPCD.
Impatto del materiale sulla rigidità
Nella progettazione di strutture in lamiera, la rigidità delle parti strutturali in lamiera spesso non viene rispettata.
I progettisti strutturali spesso utilizzano acciaio a basso tenore di carbonio o acciaio inossidabile al posto dell'acciaio a basso tenore di carbonio, oppure sostituiscono la normale lega di alluminio con una lega di alluminio dura ad alta resistenza e durezza, che dovrebbe aumentare la rigidità del pezzo.
In realtà non c'è alcun effetto evidente.
Per i materiali dello stesso substrato, la resistenza e la durezza del materiale possono essere notevolmente migliorate mediante trattamento termico e lega.
Ma la variazione di rigidità è minima.
Per migliorare la rigidità del pezzo, solo modificando il materiale e la forma del pezzo si può ottenere un certo effetto.
Per il modulo elastico e il modulo di taglio di diversi materiali, vedere la Tabella 1-2.
Tabella 1-2 Modulo elastico e modulo di taglio dei materiali più comuni
Modulo elastico E | Modulo di taglio G | |
---|---|---|
Articolo | GPa | GPa |
Ghisa grigia | 118~126 | 44.3 |
Ferro duttile | 173 | |
Acciaio al carbonio, acciaio al nichel-cromo | 206 | 79.4 |
Acciaio fuso | 202 | |
Rame puro laminato | 108 | 39.2 |
Rame puro trafilato a freddo | 127 | 48 |
Bronzo fosforoso laminato | 113 | 41.2 |
Ottone trafilato a freddo | 89~97 | 34.3~36.3 |
Bronzo al manganese laminato | 108 | 39.2 |
Alluminio laminato | 68 | 25.5~26.5 |
Estrarre il filo di alluminio | 69 | |
Alluminio fuso bronzo | 103 | 11.1 |
Bronzo fuso in stagno | 103 | |
Lega di alluminio duro | 70 | 26.5 |
Zinco laminato | 82 | 31.4 |
Piombo | 16 | 6.8 |
Vetro | 55 | 1.96 |
Plexiglass | 2.35~29.4 | |
Gomma | 0.0078 | |
Bakelite | 1.96~2.94 | 0.69~2.06 |
Plastica fenolica | 3.95~8.83 | |
Celluloide | 1.71~1.89 | 0.69~0.98 |
Nylon 1010 | 1.07 | |
Tetracloroetilene duro | 3.14~3.92 | |
Politetracloroetilene | 1.14~1.42 | |
Polietilene a bassa pressione | 0.54~0.75 | |
Polietilene ad alta pressione | 0.147~0.24 | |
Calcestruzzo | 13.73~39.2 | 4.9~15.69 |
Confronto delle prestazioni delle piastre comunemente utilizzate
Tabella 1-3 Confronto delle prestazioni di diverse lastre comunemente utilizzate
Coefficiente di prezzo | Resistenza di giro (mΩ) | Prestazioni di lavorazione della punzonatura CNC | Elaborazione laser prestazioni | Prestazioni di piegatura | Tecnologia dei dadi per rivetti | Tecnologia dei rivetti a pressione | Rivestimento superficiale | Prestazioni di protezione dell'incisione |
---|---|---|---|---|---|---|---|---|
1 | buono | buono | buono | buono | buono | Media | Molto buono | |
1.2 | 27 | buono | buono | buono | buono | buono | Media | buono |
1.7 | 26 | buono | buono | buono | buono | buono | Media | più povero |
1.3 | 26 | buono | buono | buono | buono | buono | Media | relativamente povero |
1.4 | 23 | buono | buono | buono | buono | buono | Media | povero |
6.5 | 60 | povero | buono | media | povero | molto scarso | povero | buono |
2.9 | 46 | Media | estrema povertà | buono | buono | buono | Media | buono |
3 | 46 | Media | estrema povertà | estrema povertà | buono | buono | Media | buono |
5.6 | buono | estrema povertà | buono | buono | buono | Media | buono | |
5 | buono | estrema povertà | buono | buono | buono | Media | buono |
Nota:
Piercing e la soppressione da Punzonatrice CNC
La punzonatura e la tranciatura CNC utilizzano il microcomputer a chip singolo della punzonatrice CNC per inserire in anticipo il programma di lavorazione (dimensioni, percorso di lavorazione, utensile di lavorazione, ecc.) del pezzo di lamiera, il che fa sì che la punzonatrice CNC adotti vari strumenti e una serie di comandi NC per ottenere una varietà di forme di lavorazione come punzonatura, rifilatura, formatura, ecc.
La punzonatura CNC in genere non è in grado di realizzare forature e tranciature con forme troppo complicate.
Caratteristiche:
È fondamentalmente in grado di soddisfare le esigenze di produzione di campioni in bianco.
Problemi e requisiti di attenzione:
La punzonatura CNC è generalmente adatta alla punzonatura di acciaio a basso tenore di carbonio, lamiera elettrolitica, lamiera di alluminio-zinco, lamiera di alluminio, lamiera di rame con T=3,5~4 mm o meno e lamiera di acciaio inossidabile con T=3 mm o meno.
Lo spessore della lamiera consigliato per la punzonatura CNC è:
Il processo di punzonatura CNC comporta una grande deformazione della lastra di rame, mentre il PC di lavorazione e la lastra di PVC presentano grandi bave sui bordi di lavorazione e una bassa precisione.
Durante la punzonatura, il diametro e la larghezza dell'utensile utilizzato devono essere superiori allo spessore del materiale. Ad esempio, un utensile con un diametro di Φ1,5 non può punzonare un materiale di 1,6 mm.
I materiali inferiori a 0,6 mm non vengono generalmente lavorati da NCT.
Materiali in acciaio inox non vengono generalmente lavorati con la NCT. (Naturalmente, il materiale da 0,6~1,5 mm può essere lavorato con NCT, ma l'usura dell'utensile è elevata e la probabilità di scarti nella lavorazione sul campo è molto più alta rispetto ad altri materiali GI).
La foratura e la tranciatura di altre forme sono auspicabilmente il più possibile semplici e uniformi.
Le dimensioni del punzone CNC devono essere normalizzate, ad esempio fori rotondi o esagonali, e la larghezza minima della scanalatura di processo è di 1,2 mm.
Piercing e la soppressione da punzonatura a freddo
Per la punzonatura e la tranciatura di pezzi di grande produzione e di piccole dimensioni, vengono realizzati e utilizzati stampi per lo stampaggio della lamiera appositamente progettati per aumentare l'efficienza della produzione.
In genere è costituito da un punzone e da una matrice.
Gli stampi sono generalmente di tipo pressato e intarsiato.
I punzoni sono generalmente: di tipo rotondo, sostituibili; di tipo combinato; di tipo a caricamento e scaricamento rapido.
Le matrici più comuni sono:
Caratteristiche:
Perché il punzonatura e tranciatura con la matrice a freddo può essere completata da una sola stampata, l'efficienza è elevata, la consistenza è buona e il costo è basso.
Pertanto, per i pezzi strutturali con una capacità di lavorazione annuale superiore a 5.000 pezzi e con dimensioni non troppo grandi, l'impianto di lavorazione esegue generalmente una lavorazione a freddo.
Nella progettazione della struttura, è necessario tenere conto della progettazione del caratteristiche del processo della lavorazione a freddo dello stampo.
Ad esempio, i pezzi non devono avere angoli vivi (tranne che per l'uso). Devono essere progettati in modo da essere arrotondati per migliorare la qualità e la durata dello stampo e rendere il pezzo bello, sicuro e durevole.
Per soddisfare i requisiti funzionali, la forma strutturale del pezzo può essere progettata in modo più complicato.
Foratura con il punzone a fori fitti
Il punzone a fori fitti può essere considerato una sorta di punzone a controllo numerico. Per i pezzi con un gran numero di fori densi, è possibile migliorare l'efficienza e la precisione della punzonatura.
Uno stampo di punzonatura appositamente realizzato può praticare un gran numero di fori fitti per lavorare il pezzo.
Ad esempio: stencil di ventilazione, deflettore di ingresso e uscita dell'aria.
Vedere la Figura 1-1.
La parte ombreggiata nella figura è uno stampo a fori densi e il foro denso del pezzo può essere rapidamente perforato dallo stampo a fori densi. Rispetto a un solo punzone, l'efficienza migliora notevolmente.
Problemi e requisiti per i progetti di disposizione di fori densi
La progettazione del foro denso sul prodotto deve considerare che le caratteristiche di lavorazione dello stampo di punzonatura a foro denso si ripetono più volte, per cui nella progettazione della disposizione del foro denso si deve adottare il seguente principio:
Lo stampo a fori fitti della Figura 1-1 a può essere progettato come illustrato nella Figura 1-4.
Lo stampo a fori fitti della Figura 1-1 b può essere progettato solo come illustrato nella Figura 1-5.
Quando si progetta la disposizione dei fori densi, cercare di progettare in base ai requisiti di cui sopra e di avere una certa regolarità, che è conveniente per l'apertura dello stampo del foro e ridurre il costo di stampaggio.
Altrimenti, per completare la lavorazione si possono utilizzare solo pochi punzoni o alcuni set di stampi.
Come mostrato nella Figura 1-6,
Taglio laser
Il taglio laser è una tecnologia di taglio senza contatto che utilizza la scarica di elettroni come fonte di energia per mettere a fuoco un laser come fonte di calore utilizzando un gruppo di specchi riflettenti. Questa energia luminosa ad alta densità viene utilizzata per ottenere la punzonatura e la tranciatura di parti di lamiera.
Caratteristiche:
Tuttavia, il costo è elevato, la tavola di supporto del pezzo da lavorare viene danneggiata e la superficie tagliata è facile che si depositi una pellicola di ossido, difficile da gestire.
In genere è adatto solo per la lavorazione di singoli e piccoli lotti.
Attenzione: in genere viene utilizzato solo per le lamiere d'acciaio.
Le lastre di alluminio e le lastre di rame non sono generalmente utilizzate perché il trasferimento di calore del materiale è troppo veloce e provoca la fusione intorno all'incisione, il che non garantisce la precisione e la qualità della lavorazione.
Il taglio laser La faccia finale presenta uno strato di ossido, che non può essere lavato via, e la faccia finale di taglio con requisiti speciali deve essere lucidata;
Il taglio laser di fori densi è più deformato; in genere non si usa il laser per tagliare fori densi.
Elettroerosione a filo
Il taglio a filo è un metodo di lavorazione in cui un pezzo da lavorare e un filo (filo di molibdeno, filo di rame) vengono utilizzati come polo e tenuti a una certa distanza; quando la tensione è sufficientemente alta, si forma uno spazio di scintilla e il pezzo da lavorare viene sottoposto a incisione elettrolitica. Il materiale rimosso viene trasportato dal fluido di lavoro.
Caratteristiche: elevata precisione di lavorazione, ma bassa velocità di lavorazione, costo elevato e modifica delle proprietà superficiali del materiale.
Generalmente utilizzato per la lavorazione degli stampi, non per la lavorazione dei pezzi di produzione.
Alcuni fori quadrati dei pannelli profilati non hanno angoli arrotondati che non possono essere fresati e, poiché le leghe di alluminio non possono essere tagliate con il laser, se non c'è spazio per la punzonatura, possono essere punzonate solo con l'elettroerosione a filo.
La velocità è molto lenta, l'efficienza è molto bassa e non è adatta alla produzione di massa. Il progetto dovrebbe evitare questa situazione.
Confronto tra i tre sistemi di soppressione e piercmetodi di produzione
Tabella 1-4 Confronto tra le caratteristiche di tre comuni lavorazioni di punzonatura e tranciatura
Nota: i dati seguenti sono dati per lamiere di acciaio laminate a freddo.
Laser | Taglio | Punch | |
---|---|---|---|
Materiale lavorabile | lamiera d'acciaio | Piastra di acciaio, piastra di rame, piastra di alluminio | Piastra di acciaio, piastra di rame, piastra di alluminio |
Spessore del materiale lavorabile | 1 mm ~ 8 mm | 0,6 mm ~ 3 mm | generalmente <4mm |
Dimensioni minime di lavorazione (lamiera normale laminata a freddo) | Fenditura minima 0,2 mm | Foro di punzonatura Ø≧t | Foro di punzonatura Ø≧t |
Cerchio minimo 0,7 mm | Foro quadrato bordo piccolo W≧t | Foro quadrato bordo piccolo W≧t | |
Larghezza della scanalatura lunga W≧t | Larghezza della scanalatura lunga W≧2t | ||
Distanza minima tra foro e foro, tra foro e bordo | ≧t | ≧t | ≧1t |
Preferibilmente la distanza tra i fori e i fori, i fori e i bordi | ≧1.5t | ≧1.5t | ≧1.5t |
Precisione di lavorazione generale | ±0,1 mm | ±0,1 mm | ±0,1 mm |
Intervallo di elaborazione | 2000X1350 | 2000X1350 | |
Effetto di apparizione | Bordo esterno liscio, uno strato di scaglie sulla faccia finale tagliata | Grandi bordi grezzi con bave | una piccola quantità di bordi grezzi |
Effetto curva | Forma liscia e modificabile | Bave grandi e forme regolari; | Forma liscia e modificabile |
Velocità di elaborazione | Tagliare rapidamente il cerchio esterno | Punzonatura rapida di fori densi | più veloce |
Elaborazione del testo | Acquaforte, meno profonda, dimensioni illimitate | Testo concavo stampato con simboli più profondi; le dimensioni sono limitate dallo stampo | Testo concavo stampato con simboli più profondi; le dimensioni sono limitate dallo stampo |
Formazione | non può | Concavo, controbattitore, piccolo tratto, ecc. | Può realizzare forme più complesse |
Costo di elaborazione | Più alto | Basso | Basso |
Tprogettazione tecnica di l'adisposizione
Nella produzione di grandi e medi volumi, il costo del materiale dei pezzi rappresenta una parte importante.
L'uso completo ed efficace dei materiali è un importante indicatore economico per la produzione di lamiere.
Pertanto, a condizione che i requisiti di progettazione non siano influenzati, il progettista strutturale dovrebbe sforzarsi di adottare il metodo di disposizione senza sprechi o con meno sprechi.
Come mostrato nella Figura 1-7, non vi è alcuna disposizione dei rifiuti.
Alcuni pezzi hanno una forma leggermente modificata, che può far risparmiare molto materiale.
Come mostrato nella Figura 1-8, la Figura 2 utilizza meno materiale rispetto alla Figura 1.
Lavorabilità dei pezzi tranciati
Affinché la punzonatrice CNC possa elaborare il raggio esterno, è necessario uno speciale utensile esterno. Per ridurre l'utensile del cerchio esterno, l'arrotondamento d'angolo standard di questo manuale, come mostrato nella Figura 1-9:
1) serie di arrotondamenti ad angolo retto di 90 gradi, il raggio è r2.0, r3.0, r5.0, r10
2) Il raggio dell'angolo smussato di 135 gradi è uniforme a R5,0.
La punzonatura è preferibile per utilizzare fori rotondi.
I fori rotondi devono essere selezionati in base alla serie di fori rotondi specificati nel manuale dello stampo per lamiera.
In questo modo è possibile ridurre il numero di utensili per i fori tondi e il tempo di sostituzione delle lame nella punzonatura CNC.
A causa dei limiti di resistenza del punzone, l'apertura non può essere troppo piccola. L'apertura minima è legata allo spessore del materiale.
Il diametro minimo del foro non deve essere inferiore al valore indicato nella Tabella 1-5 di seguito.
Tabella 1-5 Dimensioni minime per la punzonatura con un punzone comune
Il diametro minimo o la lunghezza minima del bordo del punzone (t è lo spessore del materiale) | |||
---|---|---|---|
Materiale | Il foro circolare D(D è il diametro). | Il foro quadrato L(L è la lunghezza del bordo). | Foro a vita, foro rettangolare a(a è la lunghezza minima del bordo). |
Acciaio ad alto e medio tenore di carbonio | ≥1.3t | ≥1.2t | ≥1t |
Acciaio a basso tenore di carbonio e ottone | ≥1t | ≥0.8t | ≥0.8t |
Alluminio, zinco | ≥0.8t | ≥0.6t | ≥0.6t |
Laminato di bakelite e tessuto | ≥0.4t | ≥0.35t | ≥0.3t |
La distanza tra i fori e tra il foro e il bordo non deve essere troppo piccola. Il valore è mostrato nella Figura 1-10:
La precisione tra il foro e la forma, il foro e la foratura elaborata dallo stampo composito è facile da garantire durante il processo di stampaggio dello stampo.
Inoltre, l'efficienza di lavorazione è elevata e il costo di manutenzione dello stampo è conveniente per la manutenzione.
Tenendo conto dei motivi di cui sopra, la distanza tra il foro e il foro, se la distanza tra il foro e la forma può soddisfare il requisito di spessore minimo della parete dello stampo in composito, il processo è migliore, come mostrato nella Figura 1-11:
Tabella 1-6 Dimensione minima del bordo della tranciatura dello stampo in materiale composito
t (<0.8 ) | t (0.8~1.59) | t (1.59~3.18) | t (>3.2) | |
---|---|---|---|---|
D1 | 3 mm | 2t | ||
D2 | 3 mm | 2t | ||
D3 | 1,6 mm | 2t | 2.5t | |
D4 | 1,6 mm | 2t | 2.5t |
Come illustrato nella Figura 1-12, prima si perfora e poi si piega. Per garantire che il foro non venga deformato, la distanza minima tra il foro e la flangia X≥2t+R
Quando si eseguono i fori sulle parti di imbutitura, vedi Figura 1-13, per garantire la forma e l'accuratezza della posizione dei fori e la resistenza dello stampo, la parete del foro e la parete diritta delle parti devono essere mantenute a una certa distanza, ovvero le distanze a1 e a2 devono soddisfare i seguenti requisiti:
Nella formula, R1, R2 è il raggio dell'angolo e t è lo spessore.
Precisione di lavorazione dei pezzi tranciati
Tabella 1-7 Tabella delle tolleranze della distanza del centro del foro (unità: mm)
Precisione di punzonatura ordinaria | Precisione di punzonatura avanzata | |||||
---|---|---|---|---|---|---|
Dimensione nominale L | Dimensione nominale L | |||||
Spessore | <50 | 50~150 | 150~300 | <50 | 50~150 | 150~300 |
<1 | ±0.1 | ±0.15 | ±0.20 | ±0.03 | ±0.05 | ±0.08 |
1~2 | ±0.12 | ±0.20 | ±0.30 | ±0.04 | ±0.06 | ±0.10 |
2~4 | ±0.15 | ±0.25 | ±0.35 | ±0.06 | ±0.08 | ±0.12 |
4~6 | ±0.20 | ±0.30 | ±0.40 | ±0.08 | ±0.10 | ±0.15 |
Nota: tutti i fori devono essere eseguiti una sola volta quando si utilizzano i valori di questa tabella.
Principio di selezione delle dimensioni di progettazione dei pezzi stampati
1) Il riferimento dimensionale di progetto del pezzo stampato è il più vicino possibile al riferimento di posizionamento prodotto, in modo da evitare l'errore di produzione della dimensione.
2) Il riferimento delle dimensioni del foro della parte stampata deve essere scelto il più lontano possibile dall'inizio alla fine del processo di stampaggio e non deve essere associato alla parte che partecipa alla deformazione.
3) Per i pezzi che vengono dispersi e stampati su stampi diversi in più fasi, è necessario utilizzare il più possibile lo stesso riferimento di posizionamento.
Tabella 1-8 Tabella delle tolleranze del centro del foro e della distanza dal bordo
Spessore | Dimensioni b | |||
---|---|---|---|---|
≤50 | 50<b≤120 | 120<b≤220 | 220<b≤360 | |
<2 | ±0.2 | ±0.3 | ±0.5 | ±0.7 |
≥2~4 | ±0.3 | ±0.5 | ±0.6 | ±0.8 |
>4 | ±0.4 | ±0.5 | ±0.8 | ±1.0 |
Nota: questa tavola è adatta alla foratura dopo la tranciatura.
Taglio secondario
Il taglio secondario è chiamato anche tranciatura secondaria o taglio supplementare (processo molto scadente, da evitare in fase di progettazione).
Il taglio secondario è che l'allungamento comporta una deformazione del materiale. Quando la deformazione di piegatura è grande, la tranciatura aumenta. Prima la formatura, poi il taglio dei fori o dei contorni per rimuovere il materiale riservato e ottenere una struttura completa di dimensioni corrette.
Applicazione: quando il bocchettone di tensionamento è vicino al bordo, è necessario eseguire un taglio supplementare.
Prendiamo ad esempio il controforo, come illustrato nella Figura 1-16.
È possibile leggi questo post per conoscere ogni dettaglio sulla piegatura della lamiera.
Le forme più comuni di dadi rivettati sono il distanziatore autobloccante, il dado autobloccante, il dado con rivetto di ancoraggio, il dado con rivetto a strappo e il dado con rivetto flottante.
Sstallo per gli elfi
La rivettatura a pressione significa che nel processo di rivettaturaSotto la pressione esterna, la parte rivettata deforma plasticamente il materiale di base e viene schiacciata nella scanalatura prefabbricata appositamente progettata nella struttura della vite e del dado rivettati, realizzando così un collegamento affidabile delle due parti.
Esistono due tipi di dadi non standard per la rivettatura: uno è un distanziatore autoagganciante e l'altro è un dado autoagganciante.
Il collegamento al substrato si ottiene con una forma rivettata.
Tali forme di rivettatura richiedono tipicamente che la parte rivettata abbia una durezza superiore a quella del substrato.
L'acciaio ordinario a basso tenore di carbonio, la lamiera in lega di alluminio e la lamiera di rame sono adatti per la crimpatura del distanziatore autobloccante.
Per le lamiere di acciaio inossidabile e di acciaio ad alto tenore di carbonio, a causa della durezza del materiale, è necessaria una speciale colonna di dadi per rivetti ad alta resistenza, che non solo è costosa, ma è anche difficile da crimpare, la crimpatura non è affidabile ed è facile che si stacchi dopo la crimpatura.
Per garantire l'affidabilità, i produttori devono spesso aggiungere saldature sul lato della colonna del dado, il che non è positivo nel processo.
Pertanto, le parti in lamiera con la colonna del dado del rivetto e il dado del rivetto non sono il più possibile in acciaio inossidabile.
Questo vale anche per le viti e i dadi a rivetto, che non sono adatti all'uso su lastre di acciaio inossidabile.
Il processo di crimpatura della colonna di dadi per rivetti è illustrato nella Figura 1-41:
Selfo che si stringe dado per rivetti
Il processo di crimpatura della vite a rivetto è illustrato nella Figura 1-42:
Adado per rivetti nchor
Per rivettatura ad ancora si intende che durante il processo di rivettatura, parte del materiale della vite o del dado rivettato si deforma plasticamente sotto l'azione di una forza esterna e si forma un accoppiamento stretto con il materiale di base, realizzando così un collegamento affidabile delle due parti.
Lo ZRS comunemente utilizzato è collegato al substrato con questo tipo di rivettatura.
Il processo di rivettatura è relativamente semplice, la resistenza del giunto è bassa e viene solitamente utilizzato per limitare l'altezza del dispositivo di fissaggio e per sopportare una piccola coppia. Come mostrato nella Figura 1-43:
Tirare dado per rivetti
La rivettatura a strappo significa che l'elemento di rivettatura si deforma plasticamente sotto l'azione di una tensione esterna durante il processo di rivettatura.
La posizione della deformazione è solitamente in una parte appositamente progettata e il substrato viene bloccato dalla porzione di deformazione per ottenere un collegamento affidabile.
I dadi a rivetto comunemente utilizzati sono collegati al substrato con questo tipo di rivettatura.
La rivettatura viene eseguita con una speciale pistola per rivetti, spesso utilizzata in luoghi in cui lo spazio di installazione è ridotto e non è possibile utilizzare strumenti di rivettatura universali, come i tubi chiusi. Come mostrato nella Figura 1-44:
Fdado per rivetti di fissaggio
Alcuni dei dadi a rivetto sulla struttura in lamiera, poiché la struttura complessiva del telaio è complessa, l'errore di accumulo della struttura è troppo grande, per cui l'errore di posizione relativa di questi dadi a rivetto è grande, il che rende difficile l'assemblaggio di altre parti.
Si tratta di un buon miglioramento dopo l'uso di un dado flottante rivettato nella posizione del dado rivettato corrispondente.
Come mostrato nella Figura 1-45: (Nota: deve esserci spazio sufficiente nella posizione di rivettatura)
Ancora rdado ivet o autobloccante dado del rivetto alla distanza laterale
Il dado del rivetto di ancoraggio o il dado del rivetto autoagglomerante vengono rivettati insieme alla lastra comprimendola.
Quando la rivettatura di ancoraggio o la rivettatura autoagganciante è troppo vicina al bordo, è facile che questa parte si deformi.
In assenza di requisiti speciali, la distanza minima tra l'asse del rivetto e il bordo della lamiera deve essere maggiore di L, vedi Figura 1-46.
In caso contrario, è necessario utilizzare morsetti speciali per evitare che i bordi della lastra vengano deformati dalla forza.
Fattori che influenzano la qualità della rivettatura
Sono molti i fattori che influenzano la qualità della rivettatura. In sintesi, sono principalmente i seguenti: prestazioni del substrato, dimensioni del foro inferiore e metodo di rivettatura.
1) Proprietà del substrato.
Quando la durezza del substrato è adeguata, la qualità della rivettatura è buona e la forza dell'elemento di rivettatura è buona.
2) Dimensioni del foro inferiore.
La dimensione del foro inferiore influisce direttamente sulla qualità della rivettatura: se l'apertura è grande, lo spazio tra il substrato e il rivetto è grande.
Per la rivettatura, la deformazione non deve essere sufficiente a riempire la scanalatura sul pezzo da rivettare, quindi la forza di taglio è insufficiente, il che influisce direttamente sulla resistenza alla spinta del dado di rivettatura (chiodo).
Per la vite a rivetto, il foro inferiore è troppo grande e la forza di pressione generata dalla deformazione plastica durante il processo di rivettatura diventa piccola, il che influisce direttamente sulla resistenza alla spinta e alla torsione della vite a rivetto (femmina).
Lo stesso vale per la rivettatura: il foro inferiore è troppo grande, quindi l'attrito effettivo tra i due pezzi dopo la deformazione plastica è ridotto, compromettendo la qualità della rivettatura.
Le dimensioni del foro inferiore sono ridotte e, sebbene la forza della rivettatura possa essere aumentata in una certa misura, la qualità estetica della rivettatura rischia di essere scarsa.
La forza di rivettatura è elevata, l'installazione è scomoda e la deformazione della piastra inferiore è facile da provocare, il che influisce sull'efficienza produttiva del lavoro di rivettatura e sulla qualità della rivettatura.
3) Metodo di rivettatura.
È stato introdotto nella sezione precedente. Le viti e i dadi di rivettatura devono prestare grande attenzione alle occasioni di utilizzo. Situazioni diverse e requisiti di forza diversi richiedono tipi diversi.
Se non viene utilizzato correttamente, riduce il campo di forza delle viti e dei dadi rivettati, causando il cedimento della connessione.
Ecco alcuni esempi che illustrano l'uso corretto della situazione normale.
1) Non installare elementi di fissaggio rivettati in acciaio o acciaio inox prima che la piastra di alluminio sia anodizzata o trattata in superficie.
2) Se la rivettatura è eccessiva sulla stessa linea retta, non c'è spazio per il flusso del materiale estruso, che genererà grandi sollecitazioni e piegherà il pezzo in una forma curva.
3) Assicurarsi che la superficie della tavola sia placcata prima di installare i rivetti.
4) I dadi M5, M6, M8, M10 sono generalmente saldati. I dadi troppo grandi richiedono generalmente un'elevata resistenza. Saldatura ad arco possono essere utilizzati. Al di sotto di M4 (incluso M4) si deve utilizzare il dado per rivetti di ancoraggio. Se è galvanizzato, è possibile utilizzare il dado per rivetti con placcatura elettrolitica.
5) Quando si rivetta il dado sul lato piegato, per garantire la qualità di rivettatura del dado rivettato, è necessario prestare attenzione a: 1.
La distanza tra il bordo del foro di rivettatura e il lato della piegatura deve essere maggiore della zona di deformazione della parte piegata. 2.
La distanza L dal centro del dado rivettato all'interno del lato piegato deve essere maggiore della somma del raggio cilindrico esterno del dado rivettato e del raggio interno della piegatura. Vale a dire, L>D/2+r.
Il saldatura a proiezione (dado per saldatura a punti) è ampiamente utilizzato nella progettazione di parti in lamiera.
Tuttavia, in molti progetti, le dimensioni del preforo non sono conformi allo standard e non possono essere posizionate con precisione.
Il tipo di struttura e le dimensioni sono quelle indicate nella Figura 1-47 e nella Figura 1-48. I valori raccomandati per il diametro del foro D0 e lo spessore H prima di saldare la piastra d'acciaio per la saldatura sono specificati nella Tabella 1-17.
Tabella 1-17 Dimensioni del dado esagonale saldato e spessore dell'apertura della piastra d'acciaio corrispondente (mm)
Dimensione della filettatura (D o D×P) | M4 | M5 | M6 | M8 | M10 | M12 | M16 | |
---|---|---|---|---|---|---|---|---|
─ | ─ | ─ | M8×1 | M10×1 | M12×1. 5 | M16×1. 5 | ||
─ | ─ | ─ | ─ | (M10×1.25) | (M12×1. 25) | ─ | ||
e | min | 9.83 | 10.95 | 12.02 | 15.38 | 18.74 | 20.91 | 26.51 |
dy | massimo | 5.97 | 6.96 | 7.96 | 10.45 | 12.45 | 14.75 | 18.735 |
min | 5.885 | 6.87 | 7.87 | 10.34 | 12.34 | 14.64 | 18.605 | |
h1 | massimo | 0.65 | 0.7 | 0.75 | 0.9 | 1.15 | 1.4 | 1.8 |
min | 0.55 | 0.6 | 0.6 | 0.75 | 0.95 | 1.2 | 1.6 | |
h2 | massimo | 0.35 | 0.4 | 0.4 | 0.5 | 0.65 | 0.8 | 1 |
min | 0.25 | 0.3 | 0.3 | 0.35 | 0.5 | 0.6 | 0.8 | |
m | massimo | 3.5 | 4 | 5 | 6.5 | 8 | 10 | 13 |
min | 3.2 | 3.7 | 4.7 | 6.14 | 7.64 | 9.64 | 12.3 | |
D0 | massimo | 6.075 | 7.09 | 8.09 | 10.61 | 12.61 | 14.91 | 18.93 |
min | 6 | 7 | 8 | 10.5 | 12.5 | 14.8 | 18.8 | |
H | massimo | 3 | 3.5 | 4 | 4.5 | 5 | 5 | 6 |
min | 0.75 | 0.9 | 0.9 | 1 | 1.25 | 1.5 | 2 |
Nota: non utilizzare il più possibile le specifiche tra parentesi.
Dimensioni comuni del foro filettato grosso
Diametro della filettatura M | Spessore t | Diametro interno D1 | Diametro esterno D2 | Altezza h | Diametro pre-punzonatura D0 | Raggio |
---|---|---|---|---|---|---|
M2.5 | 0.6 | 2.1 | 2.8 | 1.2 | 1.4 | 0.3 |
0.8 | 2.8 | 1.44 | 1.5 | 0.4 | ||
1 | 2.9 | 1.8 | 1.2 | 0.5 | ||
1.2 | 2.9 | 1.92 | 1.3 | 0.6 | ||
M3 | 1 | 2.55 | 3.5 | 2 | 1.4 | 0.5 |
1.2 | 3.5 | 2.16 | 1.5 | 0.6 | ||
1.5 | 3.5 | 2.4 | 1.7 | 0.75 | ||
M4 | 1 | 3.35 | 4.46 | 2 | 2.3 | 0.5 |
1.2 | 4.5 | 2.16 | 2.3 | 0.6 | ||
1.5 | 4.65 | 2.7 | 1.8 | 0.75 | ||
2 | 4.56 | 3.2 | 2.4 | 1 | ||
M5 | 1.2 | 4.25 | 5.6 | 2.4 | 3 | 0.6 |
1.5 | 5.75 | 3 | 2.5 | 0.75 | ||
2 | 5.75 | 3.6 | 2.7 | 1 | ||
2.5 | 5.75 | 4 | 3.1 | 1.25 |
La distanza minima dalla maschiatura al bordo di curvatura
Tabella 1-19 Distanza tra il centro della maschiatura e il bordo di piegatura Tabella di confronto dei valori H
Spessore/diametro del filetto | 1 | 1.2 | 1.5 | 2 |
---|---|---|---|---|
M3 | 6.2 | 6.6 | - | - |
M4 | 7.7 | 8 | - | |
M5 | - | 7.6 | 8.4 | - |
Tabella 1-20 Confronto tra dado a rivetto, dado autoagganciante, rivettatura a strappo e maschiatura
Metodo di connessione / funzione | Dado per rivetti di ancoraggio | dado per rivetti autobloccanti | rivettatura a strappo | flangiatura e maschiatura |
---|---|---|---|---|
Processabilità | è buono | buono | buono | media |
Requisiti della lamiera | Rivettatura in acciaio inox, facile da staccare | La rivettatura dell'acciaio inossidabile è molto scadente, è necessario utilizzare dadi speciali per rivetti e saldatura a punti | nessuno | Piastra sottile e rame, alluminio materiale morbido facile da scivolare |
Precisione | buono | buono | buono | media |
Durata | buono | buono | buono | Rame e alluminio i materiali morbidi sono scarsi, i fili di altri materiali hanno da 3 a 4 fibbie o più |
Costo | alto | alto | media | basso |
qualità | buono | buono | buono | media |
Il tratto di lamiera è illustrato nella Figura 1-50.
Considerazioni sull'allungamento della lamiera:
Per quanto riguarda la forma e le dimensioni della lamiera convessa, nel manuale dello stampo per lamiera sono specificate diverse serie. Nella libreria di Intralink è presente un modello di forma corrispondente.
Il progetto deve essere selezionato in base alle dimensioni specificate nel manuale e lo stampo Form della libreria viene utilizzato direttamente.
Dimensione limite del passo convesso e del margine convesso
Tabella 1-21 Dimensioni limite del passo e del margine convesso
Schema | L | B | D |
---|---|---|---|
![]() | 6.5 | 10 | 6 |
8.5 | 13 | 7.5 | |
10.5 | 15 | 9 | |
13 | 18 | 11 | |
15 | 22 | 13 | |
18 | 26 | 16 | |
24 | 34 | 20 | |
31 | 44 | 26 | |
36 | 51 | 30 | |
43 | 60 | 35 | |
48 | 68 | 40 | |
55 | 78 | 45 |
Come illustrato nella figura 1-52, una mezza goffratura di 0,3 pollici su lamiera può essere utilizzata come adesivo per un'etichetta o simili per migliorare l'affidabilità dell'etichetta.
Con tale semi-taglio concavo, la deformazione è molto minore rispetto al normale stiramento, ma c'è ancora una certa deformazione per una piastra di copertura di grande superficie e una piastra inferiore che non è piegata o ha una piccola altezza di flessione.
Metodo alternativo: Per migliorare la deformazione, è possibile punzonare due linee ad angolo retto nell'intervallo di etichettatura.
Tuttavia, l'affidabilità del fissaggio dell'etichetta è ridotta.
Questo metodo può essere utilizzato anche per elaborazioni quali la codifica del prodotto, la data di produzione, la versione e persino il modello.
La pressatura delle nervature sulle parti metalliche a forma di piastra, vedi Figura 1-53, contribuisce ad aumentare la rigidità strutturale.
Come mostrato nella Figura 1-54,
Il perforazione La rivettatura è un metodo di rivettatura tra lamiere, utilizzato principalmente per il collegamento di lastre di acciaio rivestite o di lastre di acciaio inossidabile.
Una delle parti è perforata, mentre l'altra è perforata e ammanettata per renderla un connettore non staccabile.
Vantaggi: la flangia è abbinata al foro diritto e ha la funzione di posizionamento. La forza di rivettatura è elevata e anche l'efficienza di rivettatura attraverso lo stampo è elevata.
Il modo specifico è quello illustrato nella Figura 1-55:
Tabella 1-22 Dimensioni di foratura e rivettatura
Parametro | Spessore T(mm) | Flangiatura altezza H(mm) | Diametro esterno flangia. D(mm) | |||||||||||
---|---|---|---|---|---|---|---|---|---|---|---|---|---|---|
No. | 3 | 3.8 | 4 | 4.8 | 5 | 6 | ||||||||
Diametro interno del foro diritto corrispondente d e foro di preforo d0 | ||||||||||||||
d | d0 | d | d0 | d | d0 | d | d0 | d | d0 | d | d0 | |||
1 | 0.5 | 1.2 | 2.4 | 1.5 | 3.2 | 2.4 | 3.4 | 2.6 | 4.2 | 3.4 | ||||
2 | 0.8 | 2 | 2.3 | 0.7 | 3.1 | 1.8 | 3.3 | 2.1 | 4.1 | 2.9 | 4.3 | 3.2 | ||
3 | 1 | 2.4 | 3.2 | 1.8 | 4 | 2.7 | 4.2 | 2.9 | 5.2 | 4 | ||||
4 | 1.2 | 2.7 | 3 | 1.2 | 3.8 | 2.3 | 4 | 2.5 | 5 | 3.6 | ||||
5 | 1.5 | 3.2 | 2.8 | 1 | 3.6 | 1.7 | 3.8 | 2 | 4.8 | 3.2 |
Nota: Con il principio generale H=T+T'+(0,3~0,4)
D = D'-0,3;
D-d=0,8T
Quando T≧0,8 mm, lo spessore della parete del foro flangiato è 0,4T.
Quando T<0,8 mm, lo spessore della parete della flangia è solitamente di 0,3 mm. H è solitamente 0,46±0,12
Nel metodo di rivettatura della lamiera, esiste anche un metodo di rivettatura che è la rivettatura Tox.
Il principio è che due pile vengono accostate, come illustrato nella Figura 1-56.
Stampaggio e imbutitura mediante stampo, utilizzato principalmente per il collegamento di lamiere di acciaio rivestite o di lamiere di acciaio inossidabile.
Presenta i vantaggi del risparmio energetico, della tutela ambientale e dell'alta efficienza.
In passato, i telai dell'industria delle comunicazioni utilizzavano maggiormente la rivettatura, ma il controllo di qualità della produzione di massa era difficile. La sua applicazione è stata ridotta e non è raccomandata.
Le dimensioni strutturali del controforo della vite sono selezionate come indicato nella tabella seguente.
Per quanto riguarda la testa svasata della vite a testa svasata, se la piastra è troppo sottile, è difficile garantire contemporaneamente la via d2 e il controforo D, e la via d2 dovrebbe essere garantita in via preferenziale.
La testa svasata e la via per le viti a testa svasata: (lo spessore della lamiera selezionata t è preferibilmente maggiore di h)
Tabella 1-23 Dimensioni del controforo della vite
![]() | d1 | M2 | M2.5 | M3 | M4 | M5 |
---|---|---|---|---|---|---|
d2 | Φ2.2 | Φ2.8 | Φ3.5 | Φ4.5 | Φ5.5 | |
D | Φ4.0 | Φ5.0 | Φ6.0 | Φ8.0 | Φ9.5 | |
h | 1.2 | 1.5 | 1.65 | 2.7 | 2.7 | |
Spessore minimo preferito | 1.2 | 1.5 | 1.5 | 2 | 2 | |
α | 90° |
Tabella 1-24 Dimensioni dei fori di svasatura per rivetti a testa svasata
![]() | d1 | Φ2 | Φ2.5 | Φ3 | Φ4 | Φ5 |
---|---|---|---|---|---|---|
d2 | Φ2.2 | Φ2.7 | Φ3.3 | Φ4.3 | Φ5.3 | |
D | Φ4.0 | Φ5.0 | Φ5.5 | Φ7.0 | Φ9.0 | |
h | 1 | 1.1 | 1.2 | 1.6 | 2 | |
α | 120° |
Il collegamento della lamiera è completato da viti a testa svasata M3.
Se lo spessore del foro placcato è di 1 mm, il metodo convenzionale è problematico.
Tuttavia, nella progettazione vera e propria, si riscontra un gran numero di problemi di questo tipo.
Di seguito viene utilizzato un dado per rivetti con un diametro di 6 mm, in grado di completare efficacemente il collegamento, come mostrato in figura.
Questo formato viene utilizzato in un gran numero di scatole di inserimento.
È importante notare che questo tipo di connessione richiede che il dado inferiore sia un dado per rivetti di ancoraggio.
Il dado autobloccante del rivetto e il maschiatore non possono completare il collegamento di serraggio.
Per standardizzare tali dimensioni, il rapporto d/D dovrebbe essere il seguente:
Tabella 1-25 Unificazione del controforo a piastra sottile
Spessore della lastra | 1 | 1.2 | 1.5 |
---|---|---|---|
M3 | 4/6 | 3.6/6.0 | 3.5/6 |
M4 | - | - | 5.8/8.8 |