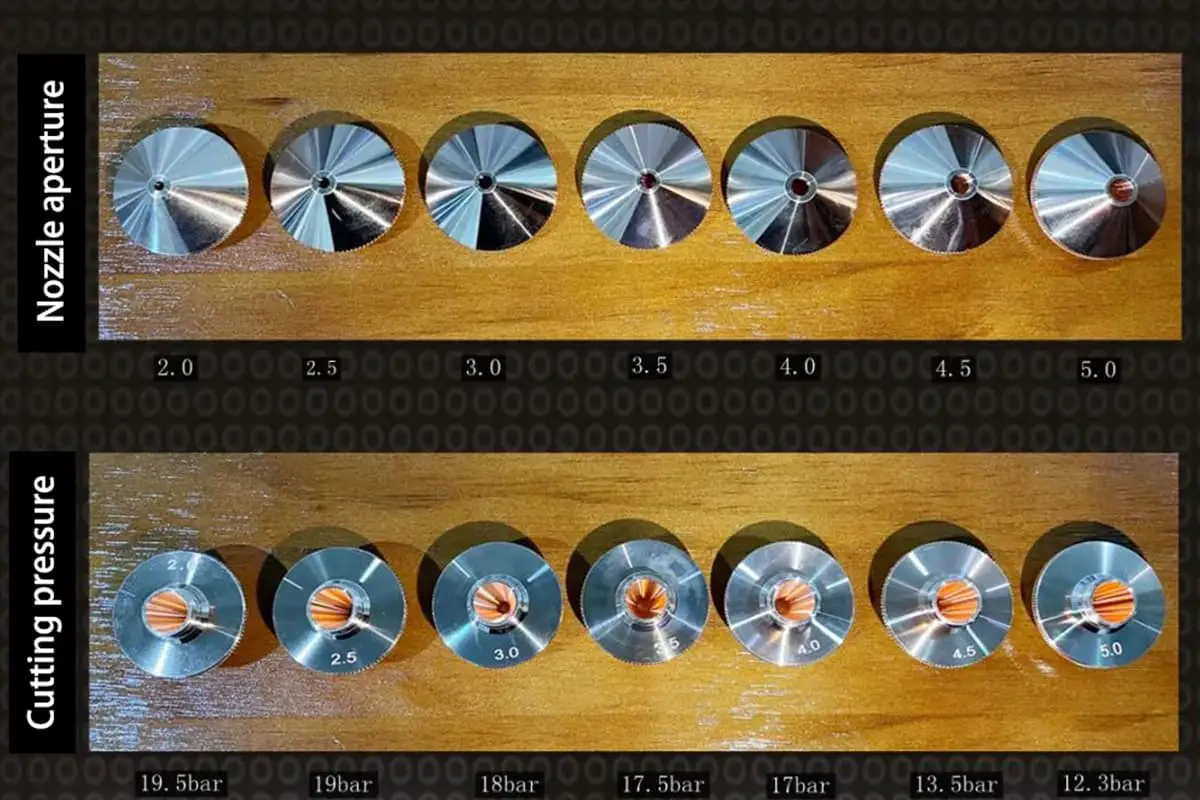
Pernahkah Anda bertanya-tanya faktor apa saja yang mempengaruhi kualitas pemotongan laser? Dalam artikel blog ini, kita akan membahas seluk-beluk interaksi laser-material dan mengeksplorasi bagaimana karakteristik sinar, daya, kecepatan, dan variabel lainnya memengaruhi hasil pemotongan. Temukan wawasan praktis dari para pakar industri untuk mengoptimalkan proses pemotongan laser Anda dan mencapai hasil yang unggul.
Proses pemotongan laser memanfaatkan kekuatan energi cahaya, mengubahnya menjadi panas yang hebat untuk melelehkan dan menguapkan bahan secara presisi.
Generator laser menghasilkan sinar dengan densitas energi tinggi, yang kemudian difokuskan melalui lensa khusus untuk menciptakan sumber energi yang sangat terkonsentrasi. Sinar terfokus ini diarahkan melalui bagian tengah nosel, yang secara simultan memancarkan gas pemotongan tambahan secara koaksial dengan jalur laser. Tindakan sinergis dari sinar laser dan gas pemotongan dengan cepat memanaskan, mengoksidasi, dan menguapkan bahan target, mencapai efek pemotongan yang diinginkan dengan akurasi yang luar biasa.
Prinsip dasar yang mendasari pemotongan laser melibatkan interaksi yang rumit antara laser dan material. Interaksi ini mencakup proses kuantum mikroskopis dan fenomena makroskopis. Hal ini mencakup penyerapan, refleksi, pembiasan, dan transmisi energi laser oleh material, serta konversi energi di dalam material. Kondisi material dan komposisi atmosfer di sekitarnya juga memainkan peran penting dalam proses ini.
Fenomena makroskopis ini, dikombinasikan dengan faktor-faktor seperti efek jaringan sinar pada permukaan material, berkontribusi pada sifat kontrol kualitas pemotongan laser yang rumit. Interaksi beragam elemen ini memerlukan kalibrasi yang tepat dan optimalisasi proses pemotongan.
Beberapa parameter utama memengaruhi kualitas pemotongan laser. Ini termasuk sifat-sifat bahan yang sedang diproses, karakteristik sinar laser (seperti panjang gelombang dan mode), output daya laser, kecepatan pemotongan, jenis dan bukaan nosel, ketinggian penyangga nosel, posisi fokus, dan jenis serta tekanan gas bantu. Masing-masing faktor ini harus dikontrol dan disesuaikan secara cermat untuk mencapai hasil pemotongan yang optimal untuk aplikasi dan bahan tertentu.
Lebar pemotongan laser terkait erat dengan mode sinar dan diameter titik fokus. Densitas daya dan energi penyinaran laser terkait dengan diameter titik laser, jadi sebaiknya memiliki diameter titik yang lebih kecil untuk mencapai densitas daya dan energi yang lebih besar dalam pemotongan laser. Ukuran diameter titik ditentukan oleh diameter output sinar laser oleh osilator dan sudut divergensinya, serta panjang fokus lensa pemfokusan.
Untuk penggunaan umum lensa pemfokusan cembung datar ZnSe dalam pemotongan laser, hubungan antara diameter titik (d), panjang fokus (ƒ), sudut divergensi (θ), dan diameter (D) sinar laser yang datang dapat dihitung dengan menggunakan rumus berikut:
(1.1)
Seperti terlihat dalam persamaan di atas, sudut divergensi yang lebih kecil dalam sinar laser akan menghasilkan diameter titik yang lebih kecil, sehingga memperbaiki efek pemotongan. Mengurangi panjang fokus lensa (ƒ) memang bermanfaat dalam mengurangi diameter titik, tetapi dengan begitu, hal ini juga memperpendek kedalaman fokus dan membuatnya sulit untuk mencapai lebar sayatan yang sama pada bagian atas dan bawah apabila memotong pelat yang lebih tebal, yang memengaruhi kualitas potongan.
Pada saat yang sama, mengurangi panjang fokus lensa, juga mengurangi jarak antara lensa dan benda kerja. Selama pemotongan, terak dapat memercik ke permukaan lensa, sehingga memengaruhi operasi pemotongan normal dan masa pakai lensa.
Lensa panjang fokus pendek memiliki densitas daya yang tinggi tetapi kedalaman fokus terbatas, sehingga cocok untuk pemotongan pelat tipis berkecepatan tinggi, selama jarak antara lensa dan benda kerja tetap konstan. Sebaliknya, lensa panjang fokus yang panjang memiliki densitas daya yang rendah tetapi kedalaman fokus yang besar, dan cocok untuk memotong bagian material yang tebal.
Sebagai aturan umum, semakin pendek panjang fokus, semakin kecil titik fokus dan semakin dangkal kedalaman fokus; sebaliknya, semakin panjang panjang fokus, semakin besar titik fokus dan semakin dalam kedalaman fokus. Contohnya, apabila panjang fokus lensa digandakan, ukuran titik fokus juga akan berlipat ganda (dari Y ke 2Y), dan kedalaman fokus akan meningkat empat kali lipat (dari X ke 4X).
Gbr.1 Fokus lensa pemfokusan
Pola sinar laser terkait dengan kemampuan pemfokusannya, yang mirip dengan ketajaman alat mekanis. Mode urutan terendah adalah TEM00, dan energi di tempat didistribusikan dengan cara seperti gaussian. Mode ini mampu memfokuskan sinar ke ukuran minimum secara teoretis, misalnya, diameter beberapa mikron, sehingga menghasilkan densitas energi yang sangat terkonsentrasi. Mode laser digambarkan dalam gambar.
Sebaliknya, sinar orde tinggi atau multi-mode memiliki distribusi energi yang lebih luas, sehingga menghasilkan titik cahaya terfokus yang lebih besar dengan densitas energi yang lebih rendah. Menggunakan jenis sinar ini untuk memotong, seperti memotong dengan pisau tumpul.
Gbr.2 Pola distribusi energi sinar
Kualitas pemotongan laser secara langsung berkaitan dengan mode sinar. Semakin rendah mode, semakin kecil ukuran titik, semakin tinggi densitas daya dan densitas energi, dan semakin baik performa pemotongan.
Sebagai contoh, ketika memotong baja karbon rendah, sinar mode TEM00 memotong 10% lebih cepat dan menghasilkan permukaan dengan kekasaran yang lebih rendah (Rz lebih rendah 10μm) dibandingkan dengan sinar mode TEM01. Dalam parameter pemotongan yang optimal, kekasaran permukaan pemotongan dapat mencapai 0,8μm.
Oleh karena itu, untuk pemotongan logamlaser mode TEM00 sering digunakan untuk mencapai kecepatan potong yang lebih cepat dan kualitas pemotongan yang lebih baik.
Ukuran kekuatan laser secara langsung mempengaruhi ketebalan pelat baja yang dapat dipotong. Semakin tinggi energinya, semakin tebal material yang dapat dipotong.
Selain itu, hal ini juga memengaruhi presisi dimensi benda kerja, lebar potongan, kekasaran permukaan potongan, dan lebar zona yang terpengaruh panas.
Kepadatan daya laser (P0, diukur dalam W/cm²) dan kepadatan energi (E0, diukur dalam J/cm²) yang disinari pada benda kerja selama proses pemotongan laser memiliki dampak yang signifikan pada proses pemotongan laser.
Apabila densitas daya laser meningkat, maka kekasaran akan berkurang. Namun demikian, apabila densitas daya (P0) mencapai nilai tertentu (kira-kira 3 x 106 W/cm²), nilai kekasaran (Rz) berhenti menurun.
Semakin besar daya laser, semakin tebal bahan yang dapat dipotong. Namun demikian, untuk daya laser yang sama, ketebalan maksimum yang dapat dipotong akan berbeda untuk bahan yang berbeda.
Tabel 1 menunjukkan ketebalan maksimum untuk Pemotongan laser CO2 dari berbagai logam untuk kekuatan laser yang berbeda.
Tabel 1 Daya laser dan ketebalan pemotongan maksimum logam
Laser CO2 | Ketebalan Pemotongan Maks / mm | ||||
---|---|---|---|---|---|
Daya / W | Baja Ringan | Baja tahan karat | Paduan Aluminium | Tembaga | Kuningan |
1500 | 12 | 9 | 3 | 1 | 2 |
1500 | 12 | - | 6 | 3 | 4 |
3000 | 22 | 12 | - | 5 | 5 |
4000 | 25 | 14 | 10 | 5 | 8 |
Untuk generator laser dengan output gelombang kontinu, ukuran dan mode daya laser akan berdampak signifikan pada kualitas pemotongan. Dalam praktiknya, daya maksimum sering ditetapkan untuk mencapai kecepatan pemotongan tercepat, meningkatkan efisiensi produksi, atau memotong bahan yang lebih tebal. Secara teori, semakin besar output, semakin baik.
Namun demikian, apabila mempertimbangkan biaya generator laser, daya output sebaiknya hanya ditetapkan mendekati daya output maksimum mesin pemotong. Gambar di bawah ini mengilustrasikan masalah yang muncul ketika memotong pelat baja karbon rendah dengan daya laser yang tidak mencukupi, seperti tidak memotong melalui (a), menghasilkan banyak terak pada bagian bawah (b), dan menghasilkan bagian yang kasar (c).
Gbr.3 Pengaruh daya laser pada kualitas pemotongan baja karbon rendah
Kecepatan potong memainkan peran penting dalam menentukan kualitas potongan pada stainless steel. pelat baja. Kecepatan pemotongan optimal menghasilkan permukaan pemotongan yang mulus dan menghilangkan terak di bagian bawah.
Jika kecepatan pemotongan terlalu cepat, hal ini dapat menyebabkan ketidakmampuan untuk memotong pelat baja sepenuhnya, sehingga menimbulkan percikan api dan terak pada bagian bawah, bahkan merusak lensa. Hal ini terjadi, karena kecepatan pemotongan yang pesat mengurangi energi per satuan luas dan logam tidak sepenuhnya meleleh.
Sebaliknya, jika kecepatan potong terlalu lambat, dapat menyebabkan pelelehan yang berlebihan, jahitan pemotongan yang lebih lebar, zona yang terpengaruh panas yang membesar, dan bahkan pembakaran benda kerja. Hal ini disebabkan karena pemotongan lambat Kecepatan memungkinkan energi terakumulasi pada mata potong, menyebabkan celah melebar, logam yang meleleh tidak dapat keluar dengan cepat, dan terak terbentuk di bagian bawah pelat baja.
Cacat ini diilustrasikan pada Gambar 4.
Gbr.4 Pengaruh kecepatan potong pada kualitas pemotongan
Kecepatan pemotongan dan daya output laser memiliki dampak langsung pada panas input benda kerja. Ini berarti, bahwa hubungan antara perubahan panas input dan kualitas pemrosesan akibat perubahan kecepatan pemotongan sama dengan hubungan antara perubahan daya output dan kualitas pemrosesan.
Biasanya, apabila kondisi pemrosesan disesuaikan, hanya satu sisi (entah daya output atau kecepatan pemotongan) yang akan diubah untuk mengubah kualitas pemrosesan, dan bukannya mengubah keduanya sekaligus.
Jenis (bentuk) nozzle dan ketinggian nozzle (jarak antara saluran keluar nozzle dan permukaan benda kerja) juga dapat memengaruhi kualitas pemotongan.
Mengontrol area difusi gas untuk mengontrol kualitas pemotongan.
Gbr.5 Pengeluaran gas dari nosel
Koaksialitas antara bagian tengah lubang saluran keluar nozzle dan sinar laser merupakan faktor krusial yang memengaruhi kualitas pemotongan. Efeknya menjadi lebih besar seiring dengan bertambahnya ketebalan benda kerja. Jika nosel berubah bentuk atau meleleh, maka secara langsung akan berdampak pada koaksialitas. Bentuk nosel dan presisi dimensi merupakan persyaratan yang tinggi, jadi penting untuk merawat nosel dan menghindari benturan yang dapat menyebabkan deformasi. Jika kondisi pemotongan berubah karena nosel yang rusak, disarankan untuk menggantinya dengan yang baru.
Jika nozzle dan laser tidak koaksial, kualitas pemotongan dapat terpengaruh sebagai berikut:
a) Efek pada bagian pemotongan
Seperti diilustrasikan dalam gambar, jika gas tambahan dihembuskan keluar dari nozzle secara tidak merata, bisa terjadi peleburan pada satu sisi dan tidak ada peleburan pada sisi lainnya. Hal ini berdampak terbatas pada pemotongan pelat tipis yang kurang dari 3mm, tetapi apabila memotong pelat yang lebih tebal dari 3mm, efeknya bisa signifikan dan dapat menyebabkan pelat tidak terpotong.
Gbr. 6 Pengaruh derajat koaksial pada bagian pemotongan
b) Dampak pada sudut tajam
Jika benda kerja memiliki sudut yang tajam atau sudut yang kecil, benda kerja akan lebih rentan terhadap pelelehan yang berlebihan dan pelat yang tebal mungkin tidak dapat dipotong.
c) Dampak pada perforasi
Perforasi bisa tidak stabil dan sulit dikendalikan, khususnya untuk pelat tebal, yang bisa menyebabkan pelelehan berlebih dan kondisi penetrasi mungkin sulit dikendalikan. Hal ini tidak banyak berpengaruh pada pelat tipis.
Posisi fokus mengacu ke jarak antara titik fokus dan permukaan benda kerja, dengan nilai yang dianggap positif jika titik fokus berada di atas permukaan dan negatif jika di bawahnya.
Gbr.7 Posisi fokus
Posisi fokus memainkan peran penting dalam menentukan lebar sayatan, kemiringan, kekasaran permukaan pemotongan, dan jumlah terak yang menempel. Posisi fokus memengaruhi diameter sinar dan kedalaman fokus objek yang diproses, yang menghasilkan perubahan pada bentuk alur dan aliran gas pemrosesan serta logam cair. Untuk menghasilkan celah yang sempit, yang penting adalah meminimalkan diameter titik fokus (d), yang sebanding dengan 4/πd^2 dan panjang fokus lensa. Kedalaman fokus yang lebih kecil menghasilkan d yang lebih kecil.
Namun demikian, pemotongan dapat menyebabkan percikan, dan lensa dapat dengan mudah rusak jika terlalu dekat ke benda kerja. Dengan demikian, panjang fokus yang banyak digunakan dalam aplikasi industri pemotongan laser daya tinggi yaitu antara 5 inci (127 mm) hingga 7,5 inci (190 mm), dengan diameter titik fokus aktual berkisar antara 0,1 hingga 0,4 mm. Sangatlah penting untuk mengontrol posisi fokus untuk mencapai hasil yang optimal.
Pada prinsipnya, mempertimbangkan berbagai faktor, seperti kualitas pemotongan dan kecepatan pemotongan:
Panjang jalur optik berbeda apabila memotong ujung proksimal dan distal dengan mesin pemotong jalur terbang, yang menyebabkan perbedaan dalam ukuran sinar sebelum pemfokusan.
Semakin besar diameter sinar yang datang, semakin kecil titik fokusnya.
Untuk meminimalkan perubahan ukuran titik fokus akibat perubahan ukuran sinar sebelum pemfokusan, sistem kompensasi jalur optik dapat dipasang untuk mempertahankan jalur optik yang konsisten pada ujung proksimal dan distal.
Sinar laser ditunjukkan melewati lensa pemfokusan pada Gambar 8.
Gbr.8 Titik fokus sinar yang melewati lensa
Diameter titik dihitung dengan rumus berikut ini:
(2)
Di antara mereka:
Selain itu, kedalaman fokus adalah faktor lain yang memengaruhi kualitas pemotongan. Rumus perhitungannya adalah sebagai berikut:
(3)
Dapat dilihat dari analisis di atas bahwa semakin dekat posisi fokus ke bagian tengah pelat baja, maka permukaan pemotongan akan semakin halus tanpa adanya terak. Pilihan posisi fokus memainkan peran penting dalam menentukan kualitas pemotongan untuk pelat baja tahan karat.
Apabila posisi fokus tepat, bahan yang sedang dipotong akan meleleh dan bahan di sepanjang tepiannya tidak meleleh, sehingga menghasilkan jahitan yang bersih dan tidak lengket, seperti diilustrasikan dalam Gambar (a).
Apabila posisi fokus tertinggal, jumlah energi yang diserap oleh bahan pemotongan per satuan luas berkurang, menyebabkan energi pemotongan melemah dan material tidak meleleh sepenuhnya dan tertiup oleh gas bantu. Hal ini menyebabkan material yang meleleh sebagian melekat pada permukaan pelat potong dan membentuk ekor terak yang tajam dan pendek, seperti yang ditunjukkan pada Gambar (b).
Apabila posisi fokus dimajukan, energi rata-rata yang diserap oleh bahan pemotongan per satuan luas meningkat, menyebabkan material yang sedang dipotong dan material di sepanjang tepi meleleh dan mengalir dalam bentuk cair. Dalam hal ini, karena tekanan dan kecepatan potong yang konstan, material yang meleleh membentuk bentuk bola dan melekat pada permukaan material, seperti yang diilustrasikan dalam Gambar (c).
Oleh karena itu, posisi fokus dapat disesuaikan dengan mengamati bentuk terak selama proses pemotongan untuk memastikan kualitas pemotongan.
Gbr.9 Pengaruh posisi fokus pada terak
Gbr.10 Pengaruh posisi fokus yang berbeda-beda pada kualitas pemotongan
Dalam produksi aktual, apabila memotong pelat baja tahan karat dengan pemotong laser, posisi fokus dipilih pada atau di dalam permukaan bahan. Hal ini dilakukan untuk meningkatkan fluiditas gas pemotongan dan bahan cair serta meningkatkan kualitas pemotongan dengan memperbesar area permukaan yang halus. Posisi fokus akan bervariasi tergantung pada ketebalan pelat baja dan harus ditentukan melalui eksperimen.
Pemilihan gas bantu (jenis dan tekanan) juga memainkan peran penting dalam menentukan kualitas pemotongan. Jenis gas, tekanan udara, diameter nozzle, dan struktur geometris dapat memengaruhi kekasaran tepi dan pembentukan gerinda. Konsumsi gas ditentukan oleh diameter nosel dan tekanan udara, dengan tekanan rendah di bawah 0,5 MPa dan tekanan tinggi di atas 2 MPa. Pengeluaran gas bantu dan sinar laser secara koaksial membantu melindungi lensa pemfokusan dari kontaminasi dan menghilangkan terak dari area pemotongan. Gas yang umum digunakan untuk pemotongan laser termasuk oksigen, nitrogen, dan udara, dengan bahan pemotongan yang berbeda, memerlukan gas tambahan yang berbeda.
Penggunaan oksigen sebagai gas bantu terutama untuk memotong baja karbon, baja tahan karat, dan bahan yang sangat reflektif melalui penyadapan dan pemotongan berkecepatan tinggi, serta untuk pemotongan oksidasi. The penggunaan mesin pemotong laser panas yang dihasilkan oleh reaksi oksidasi untuk pemotongan yang efisien, namun juga menghasilkan pembentukan lapisan oksida pada permukaan pemotongan.
Nitrogen terutama digunakan dalam pemotongan pelat baja tahan karat tanpa oksidasi dan lembaran logam galvanis tanpa terak.
Udara terutama digunakan untuk memotong aluminium dan baja galvanis tanpa terak dan untuk memotong non-logam biasa.
Tekanan gas bantu tergantung pada jenis gas yang digunakan, bahan pemotongan, ketebalan pelat, dan bentuk keluaran laser (gelombang kontinu/pulsa). Tekanan gas bantu memengaruhi perlekatan terak, kualitas permukaan potongan, dan ukuran area yang terpengaruh panas.
Kondisi tekanan udara dari saluran keluar nozzle selama pemrosesan ditunjukkan dalam tabel berikut ini:
Tabel 2 Hubungan antara proses pemotongan dan tekanan gas bantu
Menyadap | Lembaran logam Pemotongan O2 | Pemotongan O2 pelat karbon tebal | Pemotongan N2 baja tahan karat | Aluminium pemotongan udara | Pemotongan permukaan bersih resin akrilik |
---|---|---|---|---|---|
(MPa) | (MPa) | (MPa) | (MPa) | (MPa) | (MPa) |
0.02-0.05 | 0.1-0.3 | 0.05-0.1 | 0.6-1.5 | 0.6-1.0 | <0.01 |
Dalam menentukan jenis gas tambahan, ukuran tekanan gas merupakan faktor yang sangat penting.
Jika tekanan gas bantu terlalu tinggi, pusaran akan terbentuk pada permukaan benda kerja, yang akan melemahkan kemampuan aliran udara untuk menghilangkan bahan cair, menyebabkan permukaan pemotongan menjadi lebih kasar dan celah melebar.
Jika tekanan gas tambahan terlalu rendah, bahan sayatan yang meleleh tidak akan tertiup angin, yang menyebabkan pembentukan terak di bagian belakang bahan yang dipotong.
Oleh karena itu, ada nilai optimal untuk tekanan gas tambahan. Tekanan gas yang tinggi diperlukan apabila memotong bahan tipis pada kecepatan tinggi untuk mencegah terbentuknya terak pada bagian belakang sayatan. Sebaliknya, apabila ketebalan material meningkat atau kecepatan pemotongan melambat, tekanan gas harus dikurangi secara tepat.
Misalnya, ketika baja tahan karat pemotongan laser pelat, penggunaan gas bantu membantu mendinginkan area di sekeliling lapisan pemotongan, mengurangi zona yang terpengaruh panas dan mencegah kerusakan lensa akibat panas.
Selain itu, menggunakan nitrogen sebagai gas tambahan meningkatkan fluiditas logam cair.
Lihat juga:
Dalam pemesinan yang sesungguhnya, cacat pemesinan dapat disebabkan oleh parameter proses yang tidak tepat.
Dengan pengalaman puluhan tahun dalam proses pemotongan laser, penting untuk meringkas tindakan penanggulangan cacat pemotongan untuk memandu produksi aktual. Lihat lampiran untuk informasi lebih lanjut.
Lihat juga:
Cacat | Kemungkinan Alasan | Solusi |
---|---|---|
Garis traksi di bagian bawah memiliki offset yang besar. Duri di bagian bawah mirip dengan terak![]() | Kecepatan pengumpanan terlalu cepat Daya laser rendah Daya laser rendah Posisi fokus tinggi | Kurangi kecepatan pengumpanan Meningkatkan daya laser Meningkatkan tekanan Menurunkan posisi fokus |
Duri di bagian bawah mirip dengan terak, yang berbentuk tetesan dan mudah dihilangkan.![]() | Kecepatan pengumpanan terlalu cepat | Kurangi kecepatan pengumpanan. |
Tekanan udara rendah | Tingkatkan tekanan | |
Posisi fokus tinggi. | Turunkan posisi fokus | |
The duri logam dapat dihilangkan sebagai sebuah blok.![]() | Posisi fokus terlalu tinggi | Turunkan posisi fokus |
Gerinda logam di bagian bawah sulit dihilangkan. ![]() | Kecepatan pengumpanan terlalu cepat | Kurangi kecepatan pengumpanan. |
Tekanan udara rendah | Tingkatkan tekanan | |
Gas tidak murni | Gunakan gas yang lebih murni | |
Posisi fokus terlalu tinggi | Turunkan posisi fokus | |
Hanya ada duri di satu sisi. ![]() | Nosel tidak berada di tengah; | Pusatkan nosel di tengah; |
Nosel memiliki cacat. | Pasang kembali nosel. | |
Materi dikeluarkan dari atas. ![]() | Daya terlalu rendah; | Segera hentikan pemotongan untuk mencegah tebasan memercik ke dalam lensa fokus. Kemudian, tingkatkan daya dan kurangi laju pemotretan. |
Kecepatan pengumpanan terlalu cepat. | ||
Dua sisi yang baik dan dua sisi yang buruk untuk pemotongan lereng. ![]() | Reflektor terpolarisasi tidak sesuai dan pemasangannya salah. Atau reflektor terpolarisasi yang rusak dipasang pada posisi lensa defleksi. | Periksa reflektor terpolarisasi |
Periksa lensa defleksi | ||
Plasma biru, tidak memotong benda kerja.![]() | Segera hentikan pemotongan untuk mencegah percikan terak ke dalam lensa fokus. | |
Kesalahan pemrosesan gas (N2) | Gunakan O2 sebagai gas pemrosesan. | |
Kecepatan pengumpanan terlalu cepat | Kurangi laju umpan | |
Daya terlalu rendah; | Meningkatkan daya | |
Permukaan pemotongan tidak presisi. ![]() | Tekanan udara terlalu tinggi | Kurangi tekanan |
Nosel rusak | Ganti nosel | |
Diameter nosel terlalu besar | Pasang nosel yang sesuai | |
Bahannya tidak bagus | Gunakan bahan yang halus dan homogen. | |
Tanpa duri, garis traksi menjadi miring. Garis traksi miring. sayatan menjadi lebih sempit di bagian bawah. ![]() | Laju pengumpanan terlalu tinggi. | Kurangi kecepatan pengumpanan. |
Menghasilkan kawah ![]() | Tekanan udara terlalu tinggi | Kurangi tekanan |
Laju pengumpanan terlalu rendah. | Meningkatkan laju umpan. | |
Fokus terlalu tinggi | Mengurangi fokus | |
Permukaan pelat berkarat. | Gunakan bahan berkualitas lebih baik. | |
Benda kerja terlalu panas. | ||
Bahannya tidak murni | ||
Permukaan yang sangat kasar. ![]() | Fokus terlalu tinggi | Mengurangi fokus |
Tekanan udara terlalu tinggi | Kurangi tekanan | |
Laju pengumpanan terlalu rendah. | Meningkatkan laju umpan. | |
Bahannya terlalu panas | Bahan pendingin |
Cacat | Kemungkinan Alasan | Solusi |
---|---|---|
Menghasilkan duri biasa yang kecil seperti tetesan.![]() | Fokus terlalu rendah | Meningkatkan fokus |
Laju pengumpanan terlalu tinggi. | Kurangi kecepatan pengumpanan. | |
Kedua sisi menghasilkan gerinda berserabut yang panjang dan tidak beraturan, perubahan warna permukaan pelat besar. ![]() | Laju pengumpanan terlalu rendah. | Meningkatkan laju umpan. |
Fokus terlalu tinggi | Mengurangi fokus | |
Tekanan udara terlalu rendah | Tingkatkan tekanan | |
Bahannya terlalu panas | Bahan pendingin | |
Duri panjang yang tidak beraturan pada mata potong. ![]() | Tidak memusatkan nosel di tengah | Pusatkan nosel |
Fokus terlalu tinggi | Mengurangi fokus | |
Tekanan udara terlalu rendah | Tingkatkan tekanan | |
Kecepatannya terlalu rendah | Tingkatkan kecepatan | |
Tepi tajam berwarna kuning. | Nitrogen mengandung pengotor oksigen. | Gunakan nitrogen yang baik. |
Plasma diproduksi pada penampang lurus. ![]() | Laju pengumpanan terlalu tinggi. | Segera hentikan pemotongan untuk mencegah percikan dari tebasan ke lensa fokus. |
Daya terlalu rendah | Kurangi kecepatan pengumpanan. | |
Fokus terlalu rendah | Meningkatkan daya | |
Meningkatkan fokus | ||
Penyebaran sinar | Laju pengumpanan terlalu tinggi. | Kurangi kecepatan pengumpanan. |
Daya terlalu rendah | Meningkatkan daya | |
Fokus terlalu rendah | Meningkatkan fokus | |
Plasma dihasilkan di sekitar sudut. | Toleransi sudut terlalu tinggi. | Kurangi toleransi sudut. |
Modulasi terlalu tinggi | Mengurangi modulasi atau akselerasi. | |
Akselerasi terlalu tinggi | ||
Sinar menyimpang di bagian awal. | Akselerasi terlalu tinggi | Akselerasi berkurang |
Fokus terlalu rendah | Meningkatkan fokus | |
Material yang meleleh gagal dikeluarkan. | Menembus lubang bundar | |
Sayatannya kasar | Nosel rusak. | Ganti nosel |
Lensa kotor | Bersihkan lensa dan ganti jika perlu. | |
Materi dikeluarkan dari atas.![]() | Daya terlalu rendah | Segera hentikan pemotongan untuk mencegah percikan dari tebasan ke lensa fokus. |
Laju pengumpanan terlalu tinggi. | Meningkatkan daya | |
Tekanan udara terlalu tinggi | Kurangi kecepatan pengumpanan. | |
Kurangi tekanan |
Cacat | Kemungkinan Alasan | Solusi |
---|---|---|
Kedua sisi menghasilkan gerinda berserabut panjang tidak beraturan yang sulit dihilangkan.![]() | Fokus terlalu tinggi | Mengurangi fokus |
Tekanan udara terlalu rendah | Tingkatkan tekanan | |
Laju pengumpanan terlalu rendah. | Meningkatkan laju umpan. | |
Kedua sisi menghasilkan gerinda panjang yang tidak beraturan yang dapat dihilangkan dengan tangan.![]() | Laju pengumpanan terlalu rendah. | Meningkatkan laju umpan. |
Sayatannya kasar | Diameter nozzle terlalu besar. | Pasang nosel yang sesuai. |
Nosel rusak. | Ganti nosel | |
Tekanan udara terlalu tinggi | Kurangi tekanan | |
Gerinda biasa yang kecil, sulit dihilangkan. ![]() | Fokus terlalu rendah | Meningkatkan fokus |
Laju pengumpanan terlalu tinggi. | Kurangi kecepatan pengumpanan. | |
Plasma diproduksi pada penampang lurus. | Laju pengumpanan terlalu tinggi. | Kurangi kecepatan pengumpanan. |
Fokus terlalu rendah | Meningkatkan fokus | |
Penyebaran sinar | Laju pengumpanan terlalu tinggi. | Kurangi kecepatan pengumpanan. |
Plasma dihasilkan di sekitar sudut. | Toleransi sudut terlalu tinggi. | Kurangi toleransi sudut. |
Modulasi terlalu tinggi | Mengurangi modulasi atau akselerasi. | |
Akselerasi terlalu tinggi | ||
Sinar menyimpang di bagian awal. | Kecepatan pendekatan terlalu tinggi | Mengurangi kecepatan pendekatan |
Fokus terlalu rendah | Meningkatkan fokus | |
Sayatannya kasar | Nosel rusak. | Ganti nosel |
Materi dikeluarkan dari atas.![]() | Daya terlalu rendah | Segera hentikan pemotongan untuk mencegah percikan dari tebasan ke lensa fokus. |
Laju pengumpanan terlalu tinggi. | Meningkatkan daya | |
Kurangi kecepatan pengumpanan. |
Cacat | Kemungkinan Alasan | Solusi |
---|---|---|
![]() | Kecepatan terlalu cepat | Kurangi kecepatan |
Fokus terlalu rendah | Meningkatkan daya | |
Daya terlalu rendah | ||
![]() | Pusat tidak tepat | Pusat inspeksi |
Lubang pada nosel tidak mulus dan bundar. | Periksa status nosel | |
Jalur cahaya tidak lurus | Periksa jalur cahaya | |
![]() | Fokus terlalu rendah | Naikkan fokus sebesar 0,1-0,2 mm setiap kali. |
![]() | Tekanan nitrogen rendah | Meningkatkan tekanan nitrogen |
![]() | Fokus terlalu tinggi | Turunkan fokus, setiap kali menurunkan 0,1-0,2 mm. |
![]() | Kecepatan potong terlalu cepat | Kecepatan potong berkurang 50-200 mm/menit setiap kali. |
![]() | Fokus terlalu rendah | Fokus ditingkatkan 0,1-0,2 mm setiap kali. |
![]() | Nitrogen tidak murni | Periksa kemurnian nitrogen. |
Ada oksigen atau udara di dalam pipa udara. | Tingkatkan penundaan untuk membersihkan pipa udara. | |
Periksa jalur gas (tidak ada kebocoran) |
Cacat | Kemungkinan Alasan | Solusi |
---|---|---|
![]() | Bagian tengah lensa tidak tepat. | Periksa bagian tengah lensa |
Lubang nosel tersumbat atau tidak bulat. | Periksa status nosel | |
Jalur cahaya tidak lurus | Periksa jalur cahaya dan bidik target lagi. | |
![]() | Panjang pengantar baris atau pengantar tidak tepat. | Perbaiki metode perkenalan dan panjang perkenalan. |
Linear salah | Memeriksa jenis baris | |
Waktu perforasi terlalu lama. | Waktu perforasi kurang dari 2 detik. | |
Terlalu banyak panas dalam pemotongan. | Kurangi siklus kerja sebesar 2-3% setiap kali. | |
![]() | Tekanannya terlalu tinggi | Kurangi tekanan, 0,1 bar setiap kali. |
Fokus terlalu tinggi | Mengurangi daya | |
Daya terlalu tinggi | Periksa fokus lensa. | |
Bahannya tidak bagus | ||
![]() | Daya rendah | Meningkatkan daya |
Kecepatan tinggi | Kurangi kecepatan | |
Tekanan rendah | Tingkatkan tekanan | |
![]() | Kecepatan terlalu tinggi | Kurangi kecepatan |
Daya rendah | Tingkatkan siklus kerja sebesar 5-10% setiap kali. | |
Tekanannya terlalu rendah | Tambahkan daya, 100W setiap kali. | |
Tingkatkan tekanan secara bertahap, 0,1-0,2bar setiap kali. | ||
![]() | Terlalu banyak panas lokal | Mengubah urutan potongan |
Masalah material | Mengubah materi | |
![]() | Tekanannya terlalu tinggi | Kurangi tekanan sebesar 0,1-0,2bar setiap kali. |
Kecepatan terlalu tinggi | Kurangi kecepatan | |
![]() | Fokus terlalu rendah | Tingkatkan fokus, 0,1-0,2 mm per langkah. |
Tekanannya terlalu rendah | Tingkatkan tekanan, 0,1-0,2 bar per langkah. |