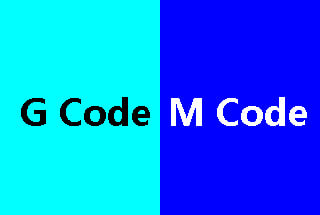
Вы испытываете трудности с качеством обработки на станках с ЧПУ? Узнайте, как небольшие изменения в технологическом процессе могут привести к значительным улучшениям. В этой статье мы рассмотрим десять советов экспертов, которые охватывают все аспекты, от выбора инструмента до методов зажима, обеспечивая высокую точность и эффективность ваших проектов по обработке. В конце статьи вы получите практические рекомендации по улучшению работы системы ЧПУ и получению превосходных результатов.
"Обработка с ЧПУ" означает использование инструментов для обработки с числовым программным управлением.
Поскольку обработка с ЧПУ контролируется компьютерным программированием, она обладает рядом преимуществ, таких как стабильное качество, высокая точность, высокая точность повторения, возможность обработки сложных поверхностей и повышенная эффективность.
Однако стоит отметить, что на конечное качество обработанного изделия может сильно повлиять человеческий фактор и опыт оператора в процессе обработки.
Давайте рассмотрим десять ценных советов по обработке, как их обобщает станок с ЧПУ оператор с более чем десятилетним опытом работы в этой области.
Разделение процессов обработки на станках с ЧПУ может быть выполнено следующими способами:
Метод сортировки, ориентированный на инструменты
Метод сортировки по инструментам заключается в разделении процессов на основе используемых инструментов и использовании одного и того же инструмента для обработки всех деталей, которые могут быть выполнены. Второй и третий ножи используются для обработки других деталей, которые они могут обработать. Такой подход сокращает количество смен инструмента, минимизирует время простоя и уменьшает количество ненужных ошибок позиционирования.
Сортировка по позиции обработки
Для деталей с большим количеством этапов обработки с ЧПУ обрабатываемая деталь может быть разделена на несколько секций в зависимости от ее структурных характеристик, таких как внутренняя форма, внешняя форма, криволинейная поверхность, плоскость и т. д. Как правило, сначала обрабатываются плоскость и позиционирующая поверхность, затем отверстия; простые геометрические формы обрабатываются раньше сложных; детали низкой точности обрабатываются раньше деталей с высокими требованиями к точности.
Сортировка по грубой и тонкой обработке с ЧПУ
Для деталей, подверженных деформации при черновой и тонкой обработке с ЧПУ, необходимо калибровать форму из-за возможной деформации после черновой обработки. Поэтому процессы грубой и тонкой обработки обычно разделяются.
В заключение следует отметить, что при разделении процесса важно учитывать структуру и технологичность деталей, функции станка, количество обрабатываемых деталей с ЧПУ, время установки и организацию производства в подразделении. Кроме того, принцип концентрации или рассредоточения процесса должен определяться исходя из реальной ситуации, но он должен быть разумным.
Последовательность обработки должна планироваться с учетом структуры и состояния деталей, а также позиционирования и зажим требования, с акцентом на избежание повреждения жесткости заготовки. При организации последовательности следует придерживаться следующих принципов:
При определении точки позиционирования и схемы зажима необходимо учитывать следующие четыре момента:
Точка установки инструмента может быть установлена на обрабатываемой детали, но важно отметить, что точка установки инструмента должна быть опорной позицией или конечным изделием. В некоторых случаях после первого процесса обработки точка установки инструмента может быть повреждена, что затрудняет определение ее местоположения в последующих процессах.
Во избежание этого следует позаботиться о том, чтобы в первом процессе установить относительную позицию установки инструмента, которая будет иметь постоянное соотношение с эталонным образцом. Таким образом, исходная точка установки инструмента может быть определена на основе относительного соотношения между ними.
Эта позиция относительной настройки инструмента часто располагается на верстаке станка или в приспособлении, и при ее выборе следует учитывать следующие принципы:
Начальная точка системы координат заготовки задается оператором. После того как заготовка надежно закреплена, настройка инструмента определяет ее положение. Она определяет расстояние между заготовкой и нулевой точкой станка.
После создания системы координат заготовки она, как правило, остается неизменной. Для обеспечения точности обработки важно, чтобы система координат заготовки и система координат программирования были синхронизированы, то есть согласовывались друг с другом в процессе обработки.
Под траекторией движения инструмента понимается траектория и направление движения инструмента относительно заготовки в процессе обработки с ЧПУ. Выбор траектории резания имеет решающее значение, так как влияет на точность и качество поверхности обработанных деталей.
При определении траектории резания учитываются следующие факторы:
После того как заготовка правильно выровнена и программа тщательно отлажена, можно переходить к этапу автоматической обработки.
На этом этапе оператор должен внимательно следить за процессом резки, чтобы не нарушить качество заготовки и предотвратить несчастные случаи, которые могут произойти в результате нештатной резки.
При контроле процесса резки необходимо учитывать следующие аспекты:
(1) На этапе черновой обработки основное внимание при контроле процесса обработки уделяется быстрому удалению лишнего материала с поверхности заготовки.
При работе станка процесс резания происходит автоматически в соответствии с заданной траекторией и параметрами резания, установленными оператором.
Оператор должен внимательно следить за изменением нагрузки резания в течение всего процесса, сверяясь с таблицей нагрузки резания. Исходя из силы опоры инструмента, следует отрегулировать параметры резания, чтобы добиться максимальной эффективности станка.
(2) Мониторинг звука резки во время процесса резки
Во время автоматического процесса резки, когда начинается процесс резки, звук инструмента, режущего заготовку, обычно стабильный, непрерывный и легкий.
На этом этапе движение станка стабильно. Однако по мере продвижения процесса резания такие проблемы, как твердые участки на заготовке, износ инструмента или неправильный зажим инструмента, могут привести к нестабильности процесса резания.
Признаками нестабильности являются изменение звука резания, столкновение инструмента с заготовкой и вибрация станка. В этих случаях необходимо оперативно скорректировать параметры и условия резания.
Если регулировка не дает желаемого результата, станок следует остановить для проверки состояния инструментов и заготовок.
(3) Контроль процесса финишной обработки для обеспечения размера заготовки и качества поверхности
В процессе чистовой обработки скорость резания высока, а скорость подачи велика. Следует обратить внимание на влияние скопления стружки на обрабатываемую поверхность.
При обработке полостей важно помнить о чрезмерном резании и износе инструмента на углах.
Для решения этих проблем можно предпринять следующие шаги:
Если эти регулировки не помогают, возможно, необходимо остановить машину и оценить целесообразность первоначальной программы.
Важно обращать внимание на положение инструмента при приостановке проверки или остановке станка. Если в режущий инструмент остановки в середине процесса резки, внезапное прекращение вращения шпинделя может привести к появлению следов от инструмента на поверхности заготовки.
В целом, рекомендуется выключать станок, когда инструмент больше не находится в состоянии резания.
(4) Мониторинг инструмента: Качество инструмента влияет на качество обработки заготовки
Качество инструмента играет важную роль в определении качества обработки заготовки.
В процессе автоматической обработки и резки нормальный износ и любые аномальные повреждения инструмента могут быть обнаружены с помощью звукового контроля, управления время резки, проверки в процессе резки и анализ поверхности заготовки.
Для того чтобы качество обработки соответствовало требуемым стандартам, необходимо своевременно управлять режущими инструментами, чтобы предотвратить любые проблемы с качеством обработки, вызванные неправильным обращением с инструментами.
(1) Для фрезерования плоскостей рекомендуется использовать нешлифованную твердосплавную концевую или торцевую фрезу. При фрезеровании в целом лучше всего использовать вторую подачу инструмента, когда это возможно. Для первой подачи инструмента рекомендуется использовать концевую фрезу для грубого фрезерования и непрерывной подачи вдоль поверхности заготовки. Рекомендуемая ширина каждой подачи инструмента должна составлять от 60% до 75% от диаметра инструмента.
(2) Концевые фрезы и концевые фрезы с твердосплавными пластинами в основном используются для обработки бобышек, канавок и поверхностей устья коробки.
(3) Шариковые и круглые фрезы (также известные как фрезы с круглым носом) обычно используются для обработки криволинейных поверхностей и контуров с переменным углом. Шариковые фрезы в основном используются для полуфинишной и финишной обработки, а круглые фрезы с цементированный карбид в основном используются для черновой обработки.
(1) Список программ обработки является важным компонентом схемы процесса обработки с ЧПУ. Он служит процедурой, которую должен соблюдать и выполнять оператор. Список программ обработки содержит подробное описание программы обработки и используется, в частности, для уточнения содержания программы, метода зажима и позиционирования, а также инструментов, выбранных для каждой программы обработки.
(2) Лист программы обработки должен содержать следующую информацию: название чертежа и файла программы, название заготовки, эскиз метода зажима, название программы, инструменты, используемые в каждой программе, максимальная глубина резания, характер обработки (например, черновая или чистовая) и теоретическое время обработки.
Прежде чем приступить к программированию, необходимо учесть следующие моменты после определения технологии обработки:
Принцип установки безопасной высоты заключается в том, чтобы она была, как правило, выше самой высокой поверхности заготовки или чтобы нулевая точка программирования была установлена на самой высокой поверхности. Это позволяет свести к минимуму риск столкновения инструмента.