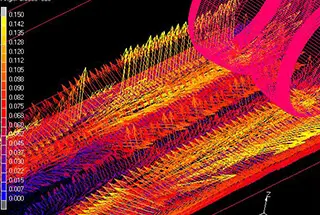
Ingenieure und Hersteller sind ständig bestrebt, Wege zur Kostensenkung zu finden, und Wasserstrahlen haben sich als äußerst effektiv erwiesen, um dieses Ziel zu erreichen und die Gewinne zu steigern.
Um die Vorteile dieser kostensparenden Technologie voll ausschöpfen zu können, ist es von entscheidender Bedeutung, ein tieferes Verständnis dafür zu erlangen, wie man Wasserstrahlschneidverfahren effektiv einsetzt, um die Kosten zu minimieren und den Gewinn zu maximieren.
Die Wasserstrahlschneideindustrie gilt als eine der vielseitigsten und am schnellsten wachsenden Industrien, wenn es um Kostensenkungsmaßnahmen geht.
Siehe auch:
Außerdem gehört der Wasserstrahlschneider zu den effizientesten Maschinen weltweit. Er übertrifft andere Schneidtechnologien wie BrennschneidenPlasmabearbeitung, Laserbearbeitung, EDM-Bearbeitung, Drehen, Fräsen und Hobeln.
Darüber hinaus ist das Wasserstrahlschneiden ein vielseitiges, effizientes und umweltfreundliches Verfahren, da es keine schädlichen Gase oder Flüssigkeiten erzeugt und keine Hitze auf der Werkstückoberfläche entsteht.
Dieses Schneidverfahren bietet einzigartige Möglichkeiten, die mit anderen einfachen Verfahren nicht erreicht werden können. Zum Beispiel können damit Löcher geschnitten werden in Titan und erzeugen komplizierte Muster auf Stein oder Glas.
Außerdem ist der Wasserstrahlschneidprozess wirklich kalt, da er beim Schneiden von Materialien keine Wärme erzeugt.
Die Überschall-Wasserpfeile, die während des Schneidprozesses erzeugt werden, führen zu hervorragenden Ergebnissen, wenn sie auf das SchneidstoffDie Kombination aus Wasser und Sand erhöht die Schneidleistung noch weiter.
Wasserstrahl, auch bekannt als "Wasser als Messer", ist der ursprüngliche Name für Hochdruck Wasserstrahlschneiden Technologie. Diese Technologie stammt aus den Vereinigten Staaten und wurde zunächst in der Luft- und Raumfahrt sowie in der Militärindustrie eingesetzt.
Seine Beliebtheit beruht auf der Tatsache, dass die physikalischen und chemischen Eigenschaften des Materials durch das Kaltschneideverfahren nicht verändert werden.
Im Laufe der Zeit und mit dem ständigen technischen Fortschritt wurden durch die Zugabe von Abrasivmitteln wie Granatsand, Diamantsand und anderen zum Hochdruckwasser die Schnittgeschwindigkeit und die Stärke des Wasserstrahlschneidens erheblich verbessert.
Die Wasserstrahltechnologie hat sich in zahlreichen Branchen durchgesetzt, darunter Keramik, Stein, Glas, Metall, Verbundwerkstoffe und andere.
In China hat der maximale Druck von Wasserstrahlen 420 MPa erreicht. Einige technologisch fortschrittliche Unternehmen haben sogar 3-Achsen- und 4-Achsen-Wasserstrahlen entwickelt, mit 5-Achsen Wasserdüsen sind eine sich schnell entwickelnde Technologie.
Der Wasserstrahl, auch als Wasserstrahlschneiden bekannt, ist eine Maschine, die Hochdruckwasser zum Schneiden verwendet. Es ermöglicht ein präzises, computergesteuertes Schneiden und wird durch die Beschaffenheit des Materials nicht wesentlich beeinträchtigt.
Aufgrund der geringen Kosten, der einfachen Bedienung und der hohen Ausbeute wird das Wasserstrahlschneiden immer mehr zum bevorzugten Schneidverfahren in der Industrietechnik.
Es kann jedes Material in einem einzigen Arbeitsgang in jede beliebige Form schneiden, was es von anderen Schneidverfahren unterscheidet, die durch Materialbeschränkungen begrenzt sind.
Beim Schneiden entsteht keine Wärme, und der Hochgeschwindigkeitsstrom des Wasserstrahls führt die entstehende Wärme sofort ab. Es entstehen auch keine schädlichen Stoffe und es hat keine thermische Wirkung auf das Material, was es zu einer umweltfreundlichen, sicheren und effizienten Schneidmethode macht.
Darüber hinaus ist keine Nachbearbeitung erforderlich, und es bietet flexible, vielseitige Schneidemöglichkeiten, mit denen sich jede gewünschte Form erzielen lässt.
UHP-Wasserschneiden, auch Wasserstrahl genannt, ist ein hochenergetischer (380MPa) Wasserstrom, der durch mehrstufige Druckbeaufschlagung von normalem Wasser erzeugt wird.
Dieses Wasser wird dann mit einer Geschwindigkeit von fast 1.000 Metern pro Sekunde durch eine hochpräzise Rubindüse (Φ0,1-0,35 mm) ausgestoßen, was es zu einem hocheffizienten Schneidverfahren macht. Dieses Schneidverfahren wird als UHP-Wasserschneiden bezeichnet.
Wasserstrahl kann in reinen Wasserstrahl und abrasiven Wasserstrahl unterteilt werden.
Der reine Wasserstrahl war die erste Methode des Wasserschneidens, deren erste kommerzielle Anwendung Mitte der 1970er Jahre mit dem Schneiden von Wellpappe begann.
Die wichtigsten Anwendungen für Reinwasser-Wasserstrahlen sind das Schneiden von Wegwerfwindeln, Baumwollpapier und Autopolsterung.
Bei Baumwollpapier und Wegwerfwindeln verursacht die Wasserstrahltechnologie im Vergleich zu anderen Technologien die geringsten Wasserrückstände.
Merkmale von Pure Water Waterjet:
Abrasive Wasserstrahlen unterscheiden sich von reinen Wasserstrahlen nur in wenigen Punkten. Beim reinen Wasserstrahl wird das Material durch den Überschallwasserstrom erodiert, während beim Abrasivwasserstrahl die Partikel des Abrasivmaterials durch die Wasserstrahlen beschleunigt werden und das Material erodieren.
Abrasive Wasserstrahlen sind hunderte oder tausende Male leistungsfähiger als reine Wasserstrahlen und werden zum Schneiden von harten Materialien wie Stahl, Stein, Verbundwerkstoffen und Keramik eingesetzt.
Mit Standardparametern können Wasserstrahl-Schleifmittel Werkstoffe mit einer Härte schneiden, die der von Aluminiumoxid-Keramik (oft als AD 99,9 bezeichnet) entspricht oder diese leicht übertrifft.
Merkmale von Abrasiv-Wasserstrahl
Wasserschneiden lässt sich anhand verschiedener Faktoren in unterschiedliche Kategorien einteilen. Dazu gehören:
Experimente haben gezeigt, dass selbst reines Wasser bestimmte empfindliche Chemikalien zur Detonation bringen kann, wenn der Wasserdruck eine bestimmte Schwelle überschreitet. Auch das Schneiden mit sandhaltigem Wasser kann aufgrund der potenziellen Energie und des Aufpralls des Schleifsandes auf den Gegenstand zur Instabilität spezieller Chemikalien führen. Der Schwellenwert wurde nach vielen Experimenten und Diskussionen auf etwa 237,6 MPa festgelegt.
Daher wird in der zerspanenden Industrie vor allem das Wasserschneiden mit einem Druck von über 200 MPa eingesetzt.
Tabelle1 Wasserstrahlschneidgeschwindigkeit für gängige Materialien
Material | Schnittstärke | Wasserdruck MPa | Öffnung der Düse Wasserschleifmittel mm | Schnittgeschwindigkeit m/min |
---|---|---|---|---|
Kohlenstoffstahl | 12 , 50 | 350 | 0.25/0.76 | 0.4, 0.1 |
Rostfreier Stahl | 13, 25 | 350 | 0.25/0.76 | 0.4, 0.2 |
Titan | 3.2, 6.4 | 350 | 0.25/0.76 | 0.8, 0.6 |
Aluminium | 12 , 100 | 350 | 0.25/0.76 | 0.6, 0.12 |
Sphäroguss | 15 | 350 | 0.25/0.76 | 0.4 |
Laminiertes Papier | 12 | 309 | 0.25 | 3.5 |
Gipskarton | 15 | 294 | 0.15 | 20 |
Gummi | 15 | 377 | 0.17 | 12 |
Silikongummi | 12 | 377 | 0.12 | 3 |
Hartgummi | 19 | 309 | 0.25 | 6 |
Stoff | 20 | 309 | 0.18 | 3 |
Faserstoff | 20 | 377 | 0.20 | 6 |
Leder | 1 | 343 | 0.15 | 30 |
Dr. Norman Franz ist weithin als der Vater der Wasserstrahltechnologie anerkannt.
Er war der erste, der die Ultrahochdruck-Wasserstrahltechnik (UHP) erforschte. Schneidewerkzeugedie als höher als 30.000 psi definiert sind. Als Forstingenieur wollte Dr. Franz eine neue Methode finden, um große Baumstämme zu Schnittholz zu verarbeiten.
Im Jahr 1950 setzte er erstmals schwere Gewichte ein, um eine Wassersäule unter Druck zu setzen, die durch eine kleine Düse gepresst wurde und einen kurzen Hochdruckstrahl erzeugte, der Holz und andere Materialien schneiden konnte.
Trotz der Schwierigkeiten, die er bei der Erzeugung eines kontinuierlichen Hochdruckstroms und der begrenzten Lebensdauer der Teile hatte, zeigte er, dass ein konvergierender Hochgeschwindigkeits-Wasserstrom eine enorme Schneidleistung hat.
Heute ist das Schneiden von Holz eine der unbedeutendsten Anwendungen für die UHP-Technologie, aber die Entdeckung von Dr. Franz hat weitreichendere Anwendungen, als er sich hätte vorstellen können.
1979 begann Dr. Mohamed Hashish von Flow Research mit der Untersuchung von Möglichkeiten zur Verbesserung der Schneidleistung von Wasserdüsen beim Schneiden von Metallen und anderen harten Materialien.
Dr. Mohamed Hashish gilt weithin als der Vater des Abrasiv-Wasserstrahls. Er hat die Methode entwickelt, einem normalen Wasserstrahl Abrasivstoffe wie Granat hinzuzufügen, so dass er fast jedes Material schneiden kann.
Im Jahr 1980 wurden Abrasivwasserstrahlen erstmals zum Schneiden von Metall, Glas und Beton eingesetzt. Im Jahr 1983 wurde das weltweit erste kommerziell verfügbare Abrasiv-Wasserstrahl-Schneidsystem eingeführt, das zunächst zum Schneiden von Autoglas eingesetzt wurde.
Die Luft- und Raumfahrtindustrie war einer der ersten Nutzer dieser Technologie, da sie deren Vorteile für die Schneiden von rostfreiem StahlTitan, hochfeste leichte Verbundwerkstoffe, die in Militärflugzeugen verwendet werden, und Kohlefaserverbundwerkstoffe in zivilen Flugzeugen.
Im Laufe der Zeit wurden Wasserstrahlschleifmaschinen von vielen anderen Branchen übernommen, z. B. von Herstellern von Stein und Fliesen, Glas, Düsentriebwerken, dem Baugewerbe, der Nuklearindustrie, Werften und vielen anderen.
Die Entwicklung des Wasserstrahlschneidens lässt sich grob in mehrere Phasen unterteilen: die Forschungs- und Versuchsphase in den frühen 1960er Jahren, die hauptsächlich im Niederdruck-Wasserstrahlbergbau und bei der Reinigung von Ölpipelines zum Einsatz kam; die Phase der Entwicklung und Erforschung von Grundausrüstungen Ende der 1960er bis Anfang der 1970er Jahre, die sich auf die Entwicklung von Hochdruckpumpen, Druckerhöhungsanlagen und Hochdruck-Rohrarmaturen konzentrierte und die Hochdruck-Wasserstrahlreinigungstechnologie förderte; die Phase der industriellen Experimente und Anwendungen von Anfang der 1970er bis Anfang der 1980er Jahre, die durch das Aufkommen einer großen Anzahl von Hochdruck-Wasserstrahlmaschinen für den Kohlebergbau, Schneidmaschinen und Reinigungsmaschinen gekennzeichnet ist; und die rasante Entwicklung von Hochdruck-Wasserstrahlen seit den 1980er Jahren, die weitere Fortschritte in der Hochdruck-Wasserstrahlforschung sowie die rasche Entwicklung neuer Technologien wie Abrasiv-Wasserstrahl, Abrasiv-Strahl, Kavitationsstrahl und selbsterregter Schockstrahl umfasst.
Gegenwärtig sind mehr als 40 Länder an der Erforschung und Anwendung der Wasserstrahltechnologie beteiligt, darunter die Vereinigten Staaten, Russland, Japan, Deutschland, die Schweiz, das Vereinigte Königreich, Frankreich, Kanada, Australien, Indien, Südkorea und Singapur.
Die Anwendung der Wasserstrahltechnologie ist recht breit gefächert und umfasst Branchen wie industrielles Schneiden, Aushub und BohrenGesteinsschneiden, Oberflächenreinigung, Materialzerkleinerung und mehr.
Das Grundprinzip eines Wasserstrahlschneiders ist einfach und komplex zugleich. Der Prozess beginnt mit einer Druckpumpe, die Wasser in ein Hochdruckrohr einleitet, das dann durch eine Schneiddüse.
Obwohl die Erklärung einfach ist, ist die Konstruktion des Schneiders kompliziert und präzise und kann einen Druck von 60.000 PSI erzeugen.
Ein kleines Leck im System kann durch Erosion dauerhafte Schäden an den Teilen verursachen. Deshalb achten Hersteller und Ingenieure sehr auf den Umgang mit Hochdruckmaterialien und den Einsatz spezieller Technik beim Zusammenbau der Maschine. Die Benutzer müssen nur ein Grundverständnis haben für wie zu bedienen der Kutter.
Abrasivschneider werden seit 1982 in verschiedenen Industriezweigen eingesetzt, unter anderem in der Automobil-, Luft- und Raumfahrt- sowie in der Glasindustrie, wobei die ersten bereits 1970 auf den Markt kamen. Im Laufe der Zeit hat sich die Präzision des Schneidens kontinuierlich verbessert.
Der Druck eines Abrasivschneiders kann bis zu 55.000 PSI erreichen, und das Hochdruckwasser tritt mit einer Geschwindigkeit von 762m/s aus einer winzigen Düse aus, was 2,5 Mal schneller ist als die Schallgeschwindigkeit.
Durch die Beimischung von Granatsand in den Hochgeschwindigkeits-Wasserstrahl wird der Schneidprozess zu einem Schleif- und Schneidprozess. Kraft und Wirkung werden durch das Wasser erzeugt, das mit 305M/s auf das zu bearbeitende Material gerichtet wird.
Zusammenfassend lässt sich sagen, dass der Wasserstrahlschneider durch die Umwandlung von mechanischer Energie aus einer Stromquelle (Motor) in Druckenergie mit Hilfe eines speziellen Geräts (z. B. einem Druckerhöhungsanschluss oder einer Hochdruckpumpe) funktioniert.
Das unter Druck stehende Wasser fließt dann durch eine kleine Düse, die die Druckenergie in kinetische Energie umwandelt und einen Hochgeschwindigkeitsstrahl bildet. Aus diesem Grund wird das Schneidgerät oft als Hochgeschwindigkeits-Wasserstrahl bezeichnet.
Hinsichtlich der Wasserqualität gibt es zwei Formen des Ultrahochdruck-Wasserschneidens (UHP): das Schneiden mit reinem Wasser, bei dem ein Schneidspalt von etwa 0,1-1,1 mm entsteht, und das Abrasivschneiden, bei dem ein Schneidspalt von etwa 0,8-1,8 mm entsteht.
Die Struktur des UHP-Wasserschneidens kann verschiedene Formen annehmen, wie z. B. eine Portalstruktur oder eine freitragende Struktur mit zwei bis drei CNC-Achsen, die typischerweise zum Schneiden von Blechen verwendet werden.
Es gibt auch eine Roboterstruktur mit fünf bis sechs CNC-Achsen, die vor allem für das Schneiden von Autoinnenteilen und Innenräumen verwendet wird.
Vorteile:
Benachteiligungen:
Hochdruck Wasserstrahl-Bearbeitung
Bei der Hochdruck-Wasserstrahlbearbeitung wird Wasser oder eine Flüssigkeit mit Zusatzstoffen verwendet, die von einem Kompressor über eine Wasserpumpe unter Druck gesetzt wird.
Diese Hochdruckflüssigkeit fließt dann gleichmäßig durch einen Flüssigkeitsspeicher und bildet schließlich einen Hochgeschwindigkeits-Flüssigkeitsstrom von 300-900 Metern pro Sekunde durch die Düse, der dann auf die Oberfläche des Werkstücks gesprüht wird, um Material abzutragen und zu bearbeiten.
Abrasive Strahlbearbeitung
Abrasive Jet Machining (AWM) ist ein Verfahren, bei dem ein Hochgeschwindigkeitsstrahl aus Mikroschleifmitteln und Hochdruckluft oder anderen Gasen eingesetzt wird.
Das Material auf der Oberfläche des Werkstücks wird durch den Hochgeschwindigkeitsaufprall und die Erosion der Schleifmittel, die durch eine speziell entwickelte Düse zugeführt werden, abgetragen und verändert.
Abrasive Wasserstrahl-Bearbeitung
Die Abrasiv-Wasserstrahl-Bearbeitung (AWJ) ist ein Verfahren, bei dem Wasser als Medium verwendet und durch eine Hochdruckerzeugungsvorrichtung hoher Druck erzeugt wird.
Der Hochdruckwasserstrahl wird dann über eine Zuführ- und Mischvorrichtung mit dem Strahlmittel vermischt, um einen zweiphasigen Flüssigkeits-Feststoff-Strahl zu bilden. Er entfernt und verändert das Oberflächenmaterial des Werkstücks durch den Hochgeschwindigkeitsaufprall und das Scheuern des Schleifmittels und des Hochdruckwasserstrahls.
Zu den Vorteilen von AWJ gehören die hohe Anpassungsfähigkeit, der große Schneidbereich, die Verfügbarkeit von Wasser und Abrasivmitteln sowie die niedrigen Kosten. Ein weiterer Vorteil ist die Umweltfreundlichkeit ohne schädliche Gase, Staub, Rauch oder Verschmutzung.
Mehrere Schneidköpfe können gleichzeitig arbeiten, um ein schnelles und effizientes Schneiden zu ermöglichen, und der Prozess ist flexibel und vielseitig für die Bearbeitung komplexer Teile.
Darüber hinaus gibt es eine gute Arbeitsumgebung ohne Vorrichtungen, eine einfache Bedienung und eine glatte Schnittfläche ohne Grate. Die Kaltbearbeitung hat keinen Einfluss auf die physikalischen und mechanischen Eigenschaften oder die intergranulare Struktur des Materials.
Insgesamt kombiniert AWJ die Vorteile von Abrasiv- und Wasserstrahl, erweitert den Bearbeitungsbereich und liefert hervorragende Ergebnisse.
Der Wasserstrahl kann in die folgenden drei Typen unterteilt werden:
Klassifizierung von Strahltechniken:
Der Impulsstrahl ist ein intermittierender Strahl, dessen Aussehen dem einer Kugel ähnelt. Er wird durch die folgenden Methoden erzeugt:
(1) Eine plötzliche Freisetzung von gespeicherter Energie oder Wasser aus einer Kanone;
(2) Druckextrusion;
(3) Durchflussregelung, auch bekannt als "Wasserschlag".
Die Leistung dieses Düsentyps hängt von Faktoren wie der Häufigkeit der Wasserschlagbildung, dem Verhältnis zwischen der Länge des Wasserschlags und dem Düsendurchmesser sowie der Energie des Wasserschlags ab.
Der Kavitationsstrahl ist eine Art Dauerstrahl, der Kavitationsblasen auf natürliche Weise innerhalb des Strahls erzeugt. Dieser Prozess stimuliert das Wachstum von Kavitationskernen oder Blasen in der Flüssigkeit, die in den Strahl gezogen werden und weiter wachsen, bis sie mit der zu reinigenden oder zu schneidenden Oberfläche kollidieren und zerbrechen.
Während des Brechvorgangs werden extrem hohe Drücke und Mikrostrahlen erzeugt, deren Spannungen die Zugfestigkeit der meisten Materialien übersteigen.
Die Vorteile der abrasiven Wasserstrahlbearbeitung sind
Der Ultrahochdruck-Wasserstrahl kann alle Arten von dicken und harten Materialien schneiden, wie Edelstahl, Aluminium, Kupfer, Stahl, Marmor, legiertes Metall, Glas, Kunststoff, Keramik, Fliesen und alle Arten von sichtbaren Materialien.
Beim Hochdruckwasserstrahlschneiden wird ein Hochgeschwindigkeitsstrahl mit hoher kinetischer Energie verwendet, der auch als Hochgeschwindigkeits-Wasserstrahlverfahren bezeichnet wird. Es handelt sich dabei um eine Art der Hochenergie-Strahlbearbeitung, ähnlich wie bei der Laser-, Ionen- und Elektronenstrahlbearbeitung.
Als neue und innovative Technologie hat das Hochdruckwasserstrahlschneiden die Schneidindustrie revolutioniert und bietet ein breites Spektrum an Anwendungsmöglichkeiten.
Mit dem Fortschritt der Technologie und der Überwindung bestimmter Einschränkungen ist das Hochdruckwasserstrahlschneiden zu einer Ergänzung anderer Schneidverfahren geworden.
Die Technologie ist in verschiedenen Branchen weit verbreitet, u. a. in der Luft- und Raumfahrt, im Automobilbau, im Maschinenbau, im Baugewerbe, in der Medizintechnik, in der elektronischen Energieversorgung, in der chemischen Industrie, bei Sportartikeln, im Militär und in der neue Materialien-verwandten Bereichen.
In der Luft- und Raumfahrtindustrie wird das Hochdruckwasserstrahlschneiden eingesetzt, um eine Vielzahl von Legierungen und neuen Materialien wie Kohlefaserverbundwerkstoffe und Kunststoffglas zu schneiden, ohne dass es zu thermischen Effekten oder Beschädigungen kommt. Materialeigenschaften.
In der Automobilindustrie wird es zum Schneiden einer Reihe von Nichtmetall- und Verbundwerkstoffen verwendet, darunter Karosserieaußenverkleidungen und Türrahmen.
In der Militärindustrie wird es zur Zerstörung von Waffen und zum Schneiden von brennbaren und explosiven Anlagen eingesetzt.
Im Maschinenbau und im Bauwesen kann es zum Schneiden aller MetallartenSie sind in der Lage, nichtmetallische, spröde Kunststoffmaterialien und schwierig zu bearbeitende Materialien wie Keramik und Beton mit hoher Effizienz und Genauigkeit zu bearbeiten.
Die Wasserstrahltechnologie wird auch in der Papier- und Gummiindustrie eingesetzt, während der abrasive Wasserstrahl in der Steinindustrie, der Keramikindustrie, der Luft- und Raumfahrt und der metallverarbeitenden Industrie verwendet wird.
Insbesondere die Anwendung der Wasserstrahltechnologie in der Automobilindustrie hat mit der Entwicklung der Branche und dem Bedarf an hoher Effizienz und Genauigkeit zugenommen.
Die Kombination von Wasserstrahlgeräten und Robotern hat sich bei der Bearbeitung von Teilen für den Automobilinnenraum besonders bewährt. Das Hochdruck-Wasserrohr wird um den Roboterarm gewickelt, und der Roboterarm und das Handgelenk können die Düse des Wasserstrahlkopfes in einer geraden Linie oder in einem Bogen zur dreidimensionalen Bearbeitung bewegen.
Anwendung der Wasserstrahltechnik in der industriellen Reinigung
Die Wasserstrahltechnologie wird in verschiedenen Bereichen eingesetzt, z. B. bei der Reinigung von Spritzkabinen in der Automobilindustrie, bei der Reinigung von Wärmetauscherrohren in der petrochemischen Industrie und bei der Gummireinigung von Start- und Landebahnen, Oberflächenbehandlung für die industrielle Rostentfernung und Korrosionsschutztechnik, die Reinigung von Triebwerksteilen in der Luft- und Raumfahrtindustrie und die Reinigung von Strahlenbelastung in Kernkraftwerken.
In den letzten Jahren haben sich einige Unternehmen mit großem Erfolg der Ultrahochdrucktechnologie für die Lebensmittelkonservierung zugewandt. So hat sich beispielsweise die amerikanische Hemell Company mit ihren Ultrahochdruckgeräten einen guten Ruf in der Lebensmittelkonservierungsbranche erworben.
Die Wasserstrahltechnologie kann für die Reinigung von Autos, Hochhäusern, Start- und Landebahnen von Flughäfen, Wärmetauschern in Chemieanlagen und vielem mehr eingesetzt werden. Viele Reinigungsmaschinen und -anlagen wurden auf den Markt gebracht, und verschiedene Reinigungsunternehmen und -dienstleister sind entstanden, um den Bedürfnissen der Nutzer gerecht zu werden.
Jüngsten Forschungsergebnissen der Universität Missouri Rolla zufolge hat der Hochdruckwasserstrahl ein enormes Potenzial. Er kann Kohle zu Reinigungszwecken in feine Partikel zerkleinern und sauberen Brennstoff erzeugen, und er kann auch Holzfasern durch hydraulischen Aufschluss trennen.
Im Jahr 2002 erreichte die Flow Company in den USA mit der Einführung der Ultrahochdruck-Wasserstrahlanlage mit einem Maximaldruck von 87000mpa, die die Produktionseffizienz erheblich verbesserte und die Kosten im Vergleich zu früheren Methoden um 40% senkte, eine neue Stufe der Ultrahochdrucktechnologie.
Da sich die Wasserstrahltechnologie ständig weiterentwickelt und ausbreitet, ist ihr Wachstums- und Anwendungspotenzial grenzenlos.
Systemparameter: Druck des Wasserstrahlsystems;
Parameter der Düsenstruktur: Durchmesser der Düse, Radius der Fase, Länge des Mischrohrs, Durchmesser des Mischrohrs;
Abrasive Parameter: Abrasives Material, Partikeldurchmesser, Abrasiver Fluss, Partikelform;
Mixing-Modus: Druckantrieb oder Unterdruckabsaugung;
Mischungszustand des Abrasivs: Trockenes Pulver oder Aufschlämmung;
Schnittparameter: Vorschubgeschwindigkeit, Zielabstand, Anzahl der Schnitte, Strahlwinkel;
Materialparameter: Festigkeit, Härte, Dichte, usw.
Die Schnittgenauigkeit beim Wasserstrahlschneiden liegt in der Regel zwischen 0,1 mm und 0,25 mm, was von mehreren Faktoren abhängt, darunter die Genauigkeit der Maschine, der Größenbereich des zu schneidenden Werkstücks sowie die Dicke und das Material des Werkstücks.
Die Positioniergenauigkeit des Maschinensystems liegt in der Regel im Bereich von 0,01 mm bis 0,03 mm.
Die Größe und Dicke des zu schneidenden Materials sowie die verwendete Düse bestimmen die Breite des Schnittspalt.
Üblicherweise beträgt die Schnittfuge beim Abrasivschneiden etwa 1,0 bis 1,2 mm. Je größer der Durchmesser der Abrasivdüse ist, desto breiter wird die Schnittfuge.
Die Qualität der abgeschrägten Kante hängt von der Schnittgeschwindigkeit ab, und eine gute Schnittqualität liegt im Allgemeinen bei 0,1 mm.
Zu den beim Wasserstrahlschneiden verwendeten Schleifmitteln gehören Quarzsand, Granat, Flusssand und Diamantsand. Die Korngröße der Schleifmittel liegt im Allgemeinen zwischen 40 und 70 Maschen, wobei die Härte des Schleifmittels die Korngröße und die Schneidfähigkeit beeinflusst.
Im Allgemeinen gilt: Je höher die Härte des Schleifmittels, desto größer die Korngröße und desto stärker die Schneidfähigkeit.
Im Allgemeinen eignen sich Materialien mit komplexen Mustern, Dicke und Schwierigkeit beim Schneiden sowie zerbrechlich und hitzeempfindlich, am besten für das Wasserstrahlschneiden.
Für das Schneiden und Bohren der Kanten eines Werkstücks ist die Verwendung eines Abrasivfräsers im Vergleich zu Sacklöchern, Bohren und Gewindeschneiden viel schneller, einfacher zu organisieren und kostengünstiger.
Das liegt daran, dass wir das Werkstück in einem einzigen Durchgang mit dem Wasserstrahl schneiden können, ohne dass das Metall in Stücke geschliffen werden muss.
Wenn es darum geht, präzise Werkstücke zu schneiden, ist der Trennschleifer ein Werkzeug, mit dem sich in einem Durchgang nahezu fertige Produkte ohne thermische Effekte herstellen lassen.
Außerdem sind die Abfälle, die ein Trennschleifer produziert, oft wertvoll, da sie in Form ganzer Stücke und nicht als Späne anfallen und wiederverwertet werden können.
Es liegt auf der Hand, dass der Prozess der Brennschneiden ist heiß und führt zu thermischen Auswirkungen auf das Endprodukt. Im Gegensatz dazu führt das Abrasivschneiden in der Regel zu einer besseren Oberflächengüte, ohne dass Schlacke auf der Rückseite des Werkstücks zurückbleibt, wodurch sich die Notwendigkeit einer Nachbearbeitung verringert.
Darüber hinaus gibt es keine Begrenzung für die zu schneidende Dicke, und die Abstände der Schnittmuster können verringert werden, um Materialkosten zu sparen.
Die erforderlichen Investitionen für Laserschneiden Ausrüstung ist erheblich. Derzeit werden sie hauptsächlich zum Schneiden von dünnen Stahlblechen und einigen Nicht-Stahlblechen verwendet.metallische Werkstoffe. Die Schnittgeschwindigkeit ist schnell und die Präzision hoch, aber es verursacht auch eine Lichtbogenmarke und thermische Effekte an der Schnittnaht.
Darüber hinaus ist das Laserschneiden für einige Materialien wie Aluminium, Kupfer und andere Nichteisenmetalle und -legierungen, insbesondere für das Schneiden dickerer Metallplatten, möglicherweise nicht geeignet, da die Schnittfläche nicht ideal ist oder sogar nicht geschnitten werden kann.
Weiterführende Lektüre: Eisenhaltige Metalle vs. Nichteisenmetalle
Gegenwärtig zielt die Forschung im Bereich der Hochleistungslasergeneratoren darauf ab, das Problem der Schneiden von dickem Stahl Platten, aber die Kosten für die Investition, die Wartung und den Betrieb der Geräte sind erheblich.
Im Gegensatz dazu hat das Wasserschneiden mehrere Vorteile, darunter niedrige Investitionskosten, wirtschaftlicher Betrieb, die Fähigkeit, eine breite Palette von Materialien zu schneiden, hohe Effizienz und einfache Bedienung und Wartung.
Wasserstrahl ist in einigen Aspekten besser als Laser
Beim Wasserstrahlschneiden gibt es keine Begrenzung für die Schnittstärke.
Auch reflektierende Materialien wie Messing und Aluminium können effektiv geschnitten werden.
Es wird keine Wärmeenergie benötigt, so dass keine Verbrennungsgefahr besteht und keine thermischen Effekte auftreten.
Bei der Anpassung der Schnittgeschwindigkeit muss nur die Schnittgeschwindigkeit geändert werden, ohne dass Gas, Fokus oder andere Komponenten verändert werden müssen.
Die Produktionskapazität kann durch die Installation mehrerer Schneidköpfe leicht erhöht werden.
Die Wartung von Lasergeräten ist spezieller und anspruchsvoller, während Wasserstrahlgeräte einen relativ geringen Wartungsaufwand erfordern.
Darüber hinaus ist die Anschaffung einer kompletten Wasserstrahlanlage kostengünstiger und kostet nur 1/2 bis 1/3 der Kosten einer Laserschneidanlage.
Plasmaschneiden hat einen erheblichen thermischen Einfluss, eine geringe Präzision, und die Schnittfläche ist nicht leicht wieder zu bearbeiten.
Andererseits ist das Wasserschneiden ein Kaltschneideverfahren, das keine thermische Verformung verursacht und zu einer hochwertigen Schnittfläche führt, ohne dass eine Nachbearbeitung erforderlich ist. Falls eine weitere Bearbeitung erforderlich ist, kann diese ebenfalls leicht durchgeführt werden.
Bei der Metallbearbeitung bietet das WEDM-Verfahren (Wire Electrical Discharge Machining) eine hohe Genauigkeit, ist aber sehr langsam in der Schnittgeschwindigkeit. In einigen Fällen sind zusätzliche Verfahren wie das Einstechen und Gewindeschneiden erforderlich.
Außerdem ist die Schnittgröße beim WEDM begrenzt. Beim Wasserstrahlschneiden hingegen kann jedes Material mit höherer Geschwindigkeit gestanzt und geschnitten werden, wobei die Flexibilität durch die variable Bearbeitungsgröße gegeben ist.
Mit dem Stanz- und Scherverfahren lassen sich einige Metallteile effizient und schnell zuschneiden, doch sind dafür spezielle Werkzeuge und Schneidevorrichtungen erforderlich.
Andererseits ist das Wasserschneiden flexibler und kann jederzeit zum Schneiden beliebig geformter Werkstücke eingesetzt werden. Dies ist vor allem beim Schneiden dicker und harter Materialien von Vorteil, da die Stanz- und Schertechnik in diesen Fällen schwierig oder unmöglich ist.
Brennschneiden ist ein gängiges Schneidverfahren in der Metallindustrie, hat aber einen großen Schnittdickenbereich und einen erheblichen thermischen Effekt, schlechte Schnittflächenqualität und Genauigkeit.
Wasserstrahlschneiden hingegen kann zum Schneiden spezieller Materialien verwendet werden, wie Legierungen mit hohem Schmelzpunkt und Verbundwerkstoffe und ist hochpräzise beim Schneiden von Platten normaler Dicke in der Glas-, Stein- und Keramikindustrie.
Wenn Laser-, Plasma-, Brenn-, Drahtschneide-, Säge-, Fräs- und andere Bearbeitungsverfahren die Bearbeitungsanforderungen erfüllen können, ist Wasserschneiden in der Regel nicht geeignet.
Die Betriebskosten des Wasserschneidens sind hoch, und importierte Verbrauchsmaterialien wie Düsen, Führungshülsen und Hochdruckdichtungen sind teuer.
Zusammenfassend lässt sich sagen, dass das Wasserschneiden zwar seine Vorteile hat, aber in bestimmten Fällen nicht geeignet ist.
Ein kompletter Satz Wasserstrahlschneidausrüstung sollte mindestens folgende Komponenten umfassen: eine Ultrahochdruckpumpe, eine Wasserstrahlschneidkopfvorrichtung, ein CNC Schneidetisch und einen Computerschaltschrank.
Die Details sind wie folgt:
Aufgrund des Energiegradienteneffekts nehmen Laser-, Autogen-, Plasma-, Strahl- und andere Schneidverfahren in dem Maße ab, wie die Schnittebene tiefer wird (weiter von der Düse entfernt).
Infolgedessen steht die geformte Schnittfläche oft nicht senkrecht zur Werkstückoberfläche, wodurch eine Schnittschräge entsteht, die ein inhärenter Fehler aller Schneidverfahren ist.
Es wurden Versuche unternommen, die Schnittneigung durch eine Erhöhung der Schneidenergie oder eine Verringerung der Schnittgeschwindigkeit zu reduzieren, aber das Problem des nicht vertikalen Schneidens kann nicht vollständig gelöst werden.
Im Jahr 1997 wurde die Idee eines schwenkbaren Schneidkopfes vorgeschlagen. Derzeit gibt es auf dem Markt kommerziell erhältliche Produkte. Diese Methode ist die direkteste und effektivste Lösung für das Problem der Schnittneigung und der Verbesserung der Genauigkeit.
Der schwenkbare Schneidkopf funktioniert durch Hinzufügen von zwei Drehachsen zur ursprünglichen dreiachsigen Plattform. Das System verwendet ein voreingestelltes Neigungsmodell und Echtzeitberechnungen der Schneidbahn.
Je nach Material und Dicke des zu schneidenden Werkstücks wird der Schneidkopf während des Schneidvorgangs kontinuierlich geschwenkt, so dass das Werkstück eine perfekte, störungsfreie Schräglage erreicht.
Pulsation: der Druck ist instabil, zum Beispiel von 150MPa auf 230MPa
Lösung:
Um das Problem zu beheben, überprüfen Sie zunächst die Pulsation des transparenten Wassereinlassrohrs, um sicherzustellen, dass sie normal ist. Wenn Sie festgestellt haben, welcher Hochdruckzylinder Probleme verursacht, bauen Sie ihn aus und prüfen Sie den Kern des Wassereinlassventils, den Sitz des Wasserauslassventils und die Feder.
In der Regel lässt sich das Problem durch die Reparatur dieser Teile beheben, aber wenn es sich nicht beheben lässt, müssen sie möglicherweise ersetzt werden. Die Feder ist ein häufiges Problem in dieser Situation.
Der Druck ist bei einem Druck stabil, aber nicht in einem normalen Zustand.
Zum Beispiel: normal 230MPa, jetzt 170Mpa oder 140MPa.
Lösung:
Prüfen Sie den Impuls der Wassereinlassleitung, um festzustellen, ob eine Verunreinigung den Kern des Wassereinlassventils in einem der Hochdruckzylinder blockiert.
Überprüfen Sie das Druckbegrenzungsventil auf Undichtigkeiten und stellen Sie fest, ob es Wasser in den kleinen Wassertank zurückführt.
Untersuchen Sie alle Teile des Hauptmotors auf eventuelle Wasserlecks.
Der Druck beträgt nur einige Dutzend Mpa, oder kein Druck
① Überprüfen Sie, ob die Wasser-, Strom- und Gasversorgung normal ist.
② Prüfen Sie, ob der Riemen rutscht oder locker ist
③ Überprüfen Sie, ob das Diamantschleifmittel hinzugefügt wurde.
④ Stellen Sie fest, ob einer der drei Hochdruckzylinder nicht funktioniert, denn wenn zwei Zylinder nicht gleichzeitig funktionieren, ist der Druck deutlich geringer oder gar nicht vorhanden.
Die abnorme Lärm von Hochdruck-Zylinder des Kurbelgehäuses, die großen Sprungbereich der Amperemeter und instabilen Druck.
Es gibt zwei mögliche Ursachen für das Geräusch:
Lösungen:
Geschnittenes Glas wird brechen
Edelstein und Sandpfeife
Die normale Lebensdauer von Edelsteinen beträgt 17 Stunden bis 7-14 Tage. Bei längerem Gebrauch kann sich die Schneidequalität verschlechtern und Symptome wie eine größere Menge an Nebel um den Schneidkopf, verstreute Wasserpfeile, Kantenausrutschen, scharfe Zähne und Unterschiede in der Druckanzeige im Vergleich zur normalen Frequenz zeigen.
Die normale Lebensdauer des Sandrohrs beträgt 3-8 Monate, je nach Qualität und Einsatzdauer. Im Laufe der Zeit kann die Düse größer werden oder ein exzentrisches Loch oder eine elliptische Form aufweisen, was dazu führt, dass das zu schneidende Werkstück eine starke Neigung, glockenförmige Ränder, einen Einbruch des Winkels und andere Probleme aufweist. Dies kann zu einer Verringerung der Werkstückgröße oder zu einem Rückgang der Schnittgeschwindigkeit führen.
Der Druck ist normal, die Wasserlinie ist normal, aber die Schneidfähigkeit ist schlecht
Ursache des Scheiterns:
Behandlungsmethode:
Der Systemdruck ist normal, aber die Schneidfähigkeit ist schlecht
Ursache des Scheiterns:
Behandlungsmethode:
Wenn der Hochdruck eingeschaltet ist, wird kein Wasser aus der Sandleitung ausgestoßen, während aus der Sandeinlassleitung Wasser ausgestoßen wird.
Ursache des Scheiterns:
Behandlungsmethode:
Die Wasserlinie ohne Sandzugabe ist normal, nach der Sandzugabe ist das Wasser divergent und die Schneidfähigkeit ist vermindert.
Ursache des Scheiterns:
Behandlungsmethode:
"Fliegender Schneidsand"
"Richtungsventil funktioniert nicht"
Wenn die oben genannten Faktoren gegeben sind, prüfen Sie, ob das Relais lose ist und ob der Schließer auf Seite 2 des Wegeventils klemmt.
"Hauptmotor arbeitet abnormal"
Wenn die Maschine wiederholt in einem Dreiecksmuster startet und stoppt, prüfen Sie, ob der vom Temperaturregler eingestellte obere Grenzdruck überschritten wurde.
"Manometer-Alarm"
"Scheitern des Kabinetts"
Nachdem Sie die oben genannten Bedingungen ausgeschlossen haben, versuchen Sie, den Notausschalter zu betätigen, indem Sie ihn alle 15 Sekunden loslassen, um zu sehen, ob die Situation behoben ist.
Ist dies nicht der Fall, unterbrechen Sie die Stromzufuhr und starten Sie das gesamte Gerät neu. Wenn das Problem weiterhin besteht, wenden Sie sich an den Hersteller.
"Großes Ventilgehäuse"
“Schalter für den Messerkopf“
Das Wasser kann nicht versiegelt werden: Nach dem Schneiden, wenn der Schalter in die zweite Position gebracht wird, stoppt der Hochdruck nicht. Dies kann zum Schleifen des Werkstücks führen, wenn die Maschine weiterläuft.
Schritte zur Fehlersuche: Prüfen Sie zunächst, ob Luft vorhanden ist. Prüfen Sie dann, ob das Luftventil richtig funktioniert.
Wenn das Problem nach der Fehlerbehebung weiterhin besteht, bauen Sie das Entlastungsventil des Messerkopfes aus und untersuchen Sie die Nadel und den Sitz auf Verschleiß oder Fehlstellung. Ersetzen Sie die verschlissenen Teile, falls erforderlich.
“Computer“
Funktioniert nicht: Wenn der Computer nicht funktioniert, lesen Sie bitte Abschnitt 5 zur Fehlerbehebung. Kann das Problem nicht behoben werden, wenden Sie sich an einen Experten für Computerwartung.
Sicherung: Für den Fall einer Systemlähmung ist auf der Festplatte eine Sicherungskopie vorhanden, die mit der Funktion "Ghost Restore mit einem Klick" wiederhergestellt werden kann.
Reparieren: Bei anderen Fehlern kann der Computer in eine Reparaturwerkstatt gebracht werden. Vergewissern Sie sich jedoch, dass das neu installierte System die Auto-CAD-Software und die Ncstudio-Schneidesoftware enthält, um eine ordnungsgemäße Funktion zu gewährleisten.
Netzwerkverbindung: Die EDV-Abteilung muss das Netzwerkkabel mit dem Internet verbinden, um eine mögliche Kontamination zu vermeiden.
Staubentfernung: Es wird empfohlen, den Computer regelmäßig zu reinigen, um Staubablagerungen zu entfernen.
"Software schneiden“
1-1) Wenn Sie beim Öffnen der Schneidesoftware die Fehlermeldung "Hardware-Selbstprüfungsfehler" erhalten, führen Sie die folgenden Schritte aus, um den Treiber zu aktualisieren:
Hinweis: Gehen Sie erst dann zum nächsten Schritt über, wenn der aktuelle Schritt abgeschlossen ist.
1-2) Wenn die Aktualisierung des Treibers das Problem nicht behebt, versuchen Sie, die Schneidesoftware neu zu installieren. Wenn das Problem weiterhin besteht, versuchen Sie es zu einem späteren Zeitpunkt erneut.
1-3) Wenn die vorangegangenen Schritte nicht zum Erfolg geführt haben, müssen Sie den Computer möglicherweise zerlegen, um das Problem zu beheben.
Wenn das Problem weiterhin besteht, versuchen Sie, die Position des Steckplatzes zu ändern und die Schritte erneut auszuführen.
2) Wenn beim Öffnen der Software keine Fehlermeldung angezeigt wird, Sie aber keine Tasten drücken oder die Schneidesoftware nicht installieren können, versuchen Sie die folgenden Schritte:
Hinweis: Bevor Sie eine neue Systeminstallation vornehmen, sollten Sie wichtige Daten und Dateien sichern.
3) Wenn die Software nicht in der Lage ist, das Gerät zu steuern, befolgen Sie diese Schritte, um das Problem zu beheben:
Hinweis: Wenn Sie das Problem nicht beheben können, wenden Sie sich an einen qualifizierten Techniker.
4) Wenn die Software immer noch nicht funktioniert, schalten Sie das Gerät aus und versuchen Sie es erneut.
5) Wenn die Zeichnung nicht geöffnet werden kann, prüfen Sie, ob sie gerade in CAD geöffnet ist. Schließen Sie CAD und öffnen Sie die gewünschte Zeichnung.
6) Ausgangsposition:
Bei der Überprüfung des ordnungsgemäßen Betriebs kann das Drücken der Not-Aus-Taste dazu führen, dass sich der Ursprung bewegt.
Wenn die XY-Achse auf ihre Grenzen hin getestet wird, kann dies auch zu einer Bewegung des Ursprungs führen. Prüfen Sie, ob sich das Werkstück bewegt oder nicht richtig befestigt ist.
7) Wenn die XY-Achse inaktiv ist:
Hinweis: Wenn das Problem weiterhin besteht, wenden Sie sich an einen qualifizierten Techniker.
10. Wartung
Verbesserung der Zuverlässigkeit und Langlebigkeit
Besonderes Augenmerk sollte auf die Verbesserung der Lebensdauer von Schlüsselkomponenten wie der Hochdruckpumpe, dem Hochdruckschlauch, dem Anschlussstück und der Düse gelegt werden.
Dies erhöht die Effizienz, verringert den Schleifmittelverbrauch und senkt den Energieverbrauch, wodurch die Kosten wettbewerbsfähiger werden.
Einführung einer intelligenten Steuerung
Die Prozessparameter können während der Bearbeitung in Echtzeit angepasst werden, um die Genauigkeit zu erhöhen. Dieser Ansatz kann für die Herstellung von Teilen mit besonderen Genauigkeitsanforderungen verwendet werden, und seine technischen und wirtschaftlichen Auswirkungen sind mit denen der Plasma- und Laserbearbeitung vergleichbar.
Ausweitung des Anwendungsbereichs
Der Anwendungsbereich der Wasserstrahlbearbeitung wird ständig erweitert, vom zweidimensionalen Schneiden und Entgraten bis hin zur Lochbearbeitung und dreidimensionalen Oberflächenbearbeitung.
Verstärkung der theoretischen Forschung
Besonderes Augenmerk sollte auf die Erstellung eines Modells für die Wasserstrahlbearbeitung und die Untersuchung der Theorie der Mehrphasenströmung gelegt werden, um das Gebiet voranzubringen.
Als Gründer von MachineMFG habe ich mehr als ein Jahrzehnt meiner Karriere der metallverarbeitenden Industrie gewidmet. Meine umfangreiche Erfahrung hat es mir ermöglicht, ein Experte auf den Gebieten der Blechverarbeitung, der maschinellen Bearbeitung, des Maschinenbaus und der Werkzeugmaschinen für Metalle zu werden. Ich denke, lese und schreibe ständig über diese Themen und bin stets bestrebt, in meinem Bereich an vorderster Front zu bleiben. Lassen Sie mein Wissen und meine Erfahrung zu einem Gewinn für Ihr Unternehmen werden.